Le Howard Hugues H-1B, le célèbre racer réalisé à partir du plan encarté RC Pilot et dessiné par Laurent BUISSYNE.
Cette maquette a été dessinée par Laurent Buissyne en 2005 au format d'un plan encarté : sa taille est donc très modeste, jugez plutôt : envergure de 152 cm,  longueur de 115 cm pour une masse de 2.400 grammes. Les aficionados de l'électrique auront compris que la motorisation était prévue pour être alimentée à partir d'un accus 3 S.
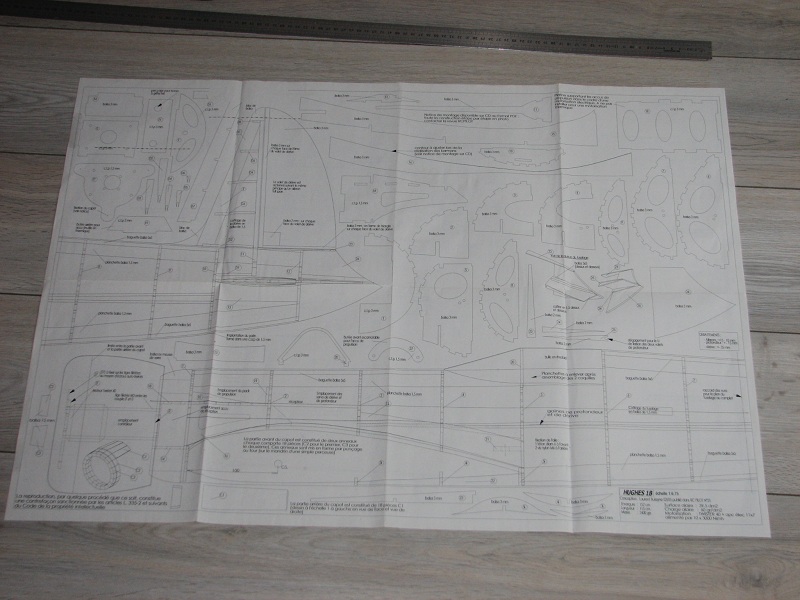
Afin d'améliorer les qualités de vol et pour faciliter l'installation des boîtiers du train rentrant
E-retract, j'ai agrandi le plan par 1,1, ce qui porte l'envergure à 168 cm.
La motorisation sera donc plus musclée et équipée d'un lipo 6 S de 4.000 mAh. Le setup est le suivant : Epower 4130-400 (Kv de 385), contrôleur de 70 A et hélice APC E 16x10. Avec une puissance de près de 1.000 watts, le Hughes 1B devrait être démonstratif.
Comme toujours pour ceux qui construisent à partir d'un plan, il est nécessaire de tout découper soi-même sauf si vous êtes équipés d'une CNC, ce qui n'est pas mon cas. Les couples sortent de planches de 30/10, avec quelques renforts en CTP.
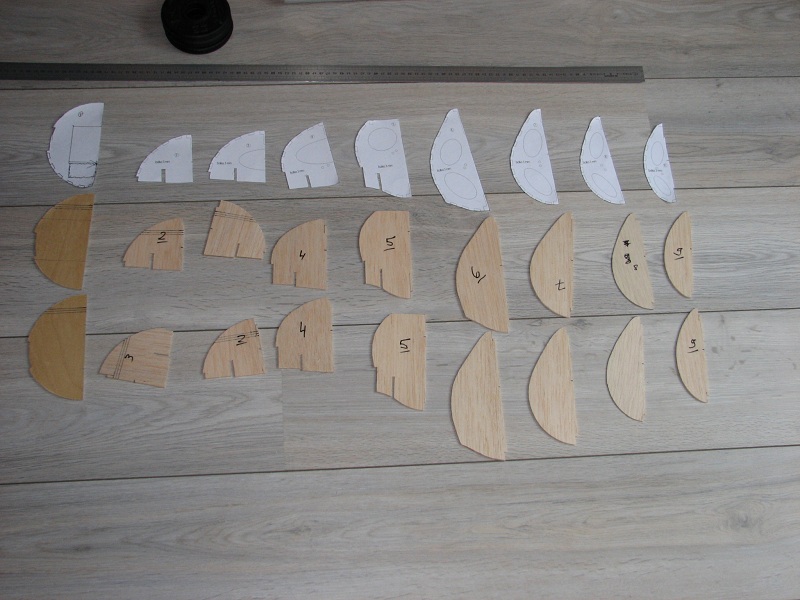
J'en ai profité pour modifier l'accès à l'accu en prévoyant les découpes nécessaires pour réaliser une trappe. C'est très classique mais il faut y penser dès le début.
La méthode de construction est donc en demi-coquilles, coffrées par des lattes découpées avec votre découpe-baguette habituel.
J'utilise de la colle Uhu Hart et après quelques heures, le fuselage  prend forme.
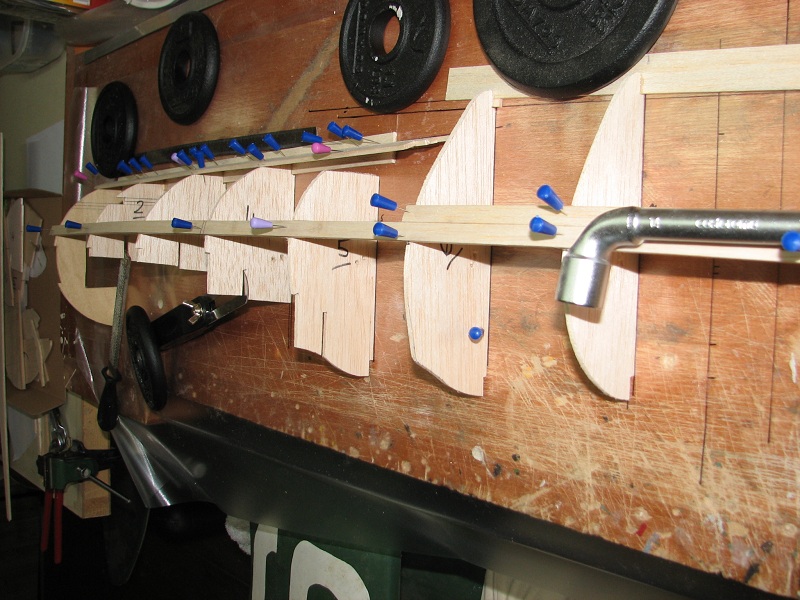
A noter que pour l'instant il n'est pas entièrement coffré pour faciliter la pose du stabilisateur et de la dérive.Â
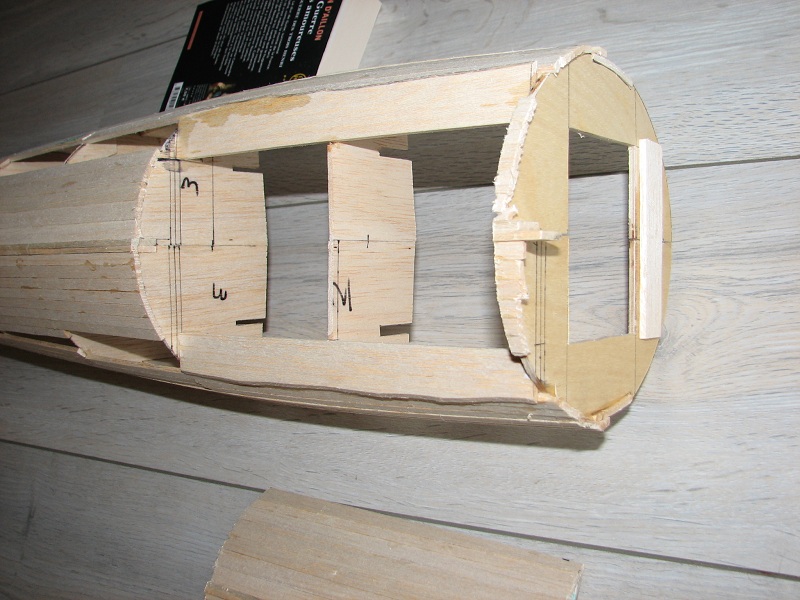
Par contre, je ne sais pas pourquoi, mais le coffrage n'est pas longiligne, il y aura du remplissage au mastic...
Le stab suit la même technique, commune aux avions Brian Taylor.
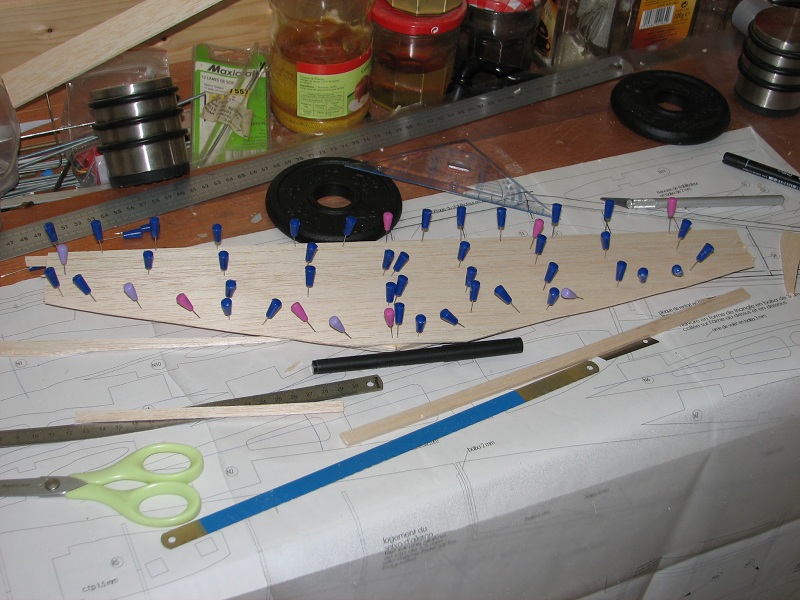
A ce stade de la construction, j'ai continué par l'aile car elle est nécessaire pour ajuster l'assise du fuselage.
Elle comporte de construction un vrillage négatif, avec des talons de nervures sur l'extrado.
Avant de commencer, il faut vérifier au moins 10 fois le positionnement du train d'atterrissage, car les boîtiers mécaniques type Kyosho ont été remplacés par ce que j'appelle la Rolls Royce des atterrisseurs, à savoir les trains électriques
E-Retract.
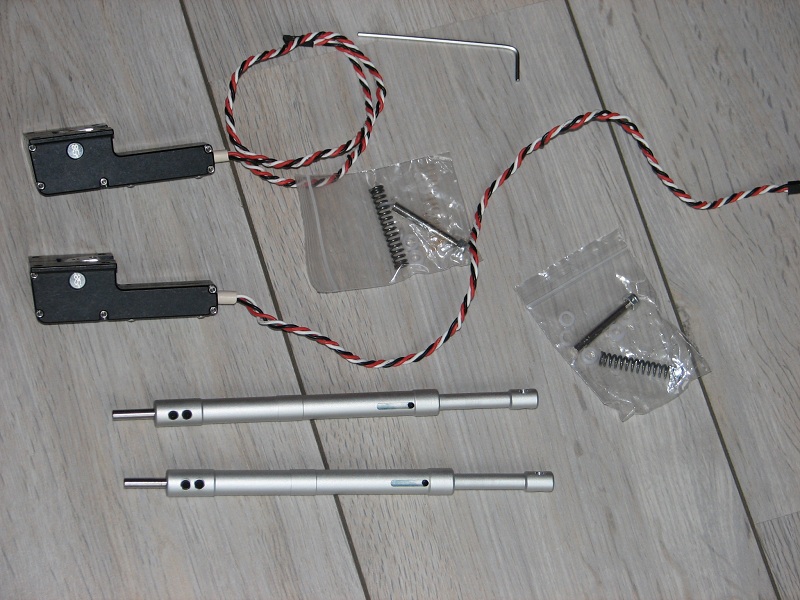
Si vous ne connaissez pas ce fabricant français, et bien, vous passez à côté de quelque chose de sensationnel !
Il existe plusieurs tailles : les modèles RS 333 prévus jusqu'à 7 kg (ceux qui équipent ce Hughes) et les RS 999 pour 15 Kg maximum.
Il suffit de choisir l'angle de sortie, de calculer la longueur des jambes amorties et de faire chauffer la carte Bleue...
Ces trains ont une durée de sortie réglable, donc hyper réaliste et dotés d'une mécanique ahurissante, sans aucun jeu. Ils se branchent tout simplement sur le récepteur, sans accu séparé.
Bref, ce que j'attendais depuis de nombreuses années. Le miracle s'est donc réalisé !
Au fait, l'équipe
E-Retract a un sens commercial et relationnel hors du commun : il suffit d'appeler Christophe ou Stéphane pour s'en convaincre...
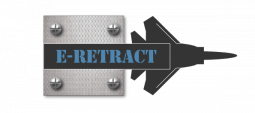
La pose des nervures sur le chantier est très classique.
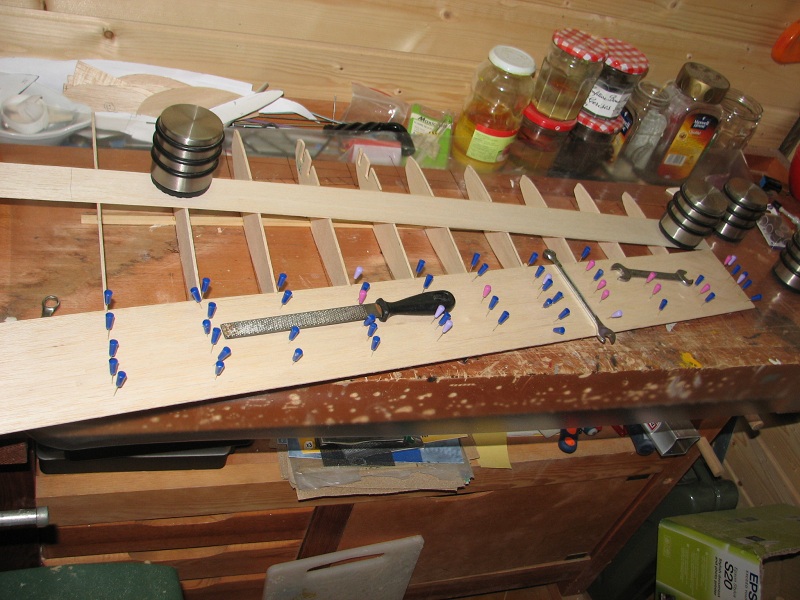
J'ai choisi l'option du coffrage intégral de l'aile car je vais l'entoiler au papier japon et enduit nitro pour faire le plus léger possible. En triant soigneusement le balsa 15/10, ce devrait être jouable.
L'aile prend vie : les baguettes de train ont été posées, trois nervures ont reçu un renfort en CTP et il reste à terminer le coffrage.
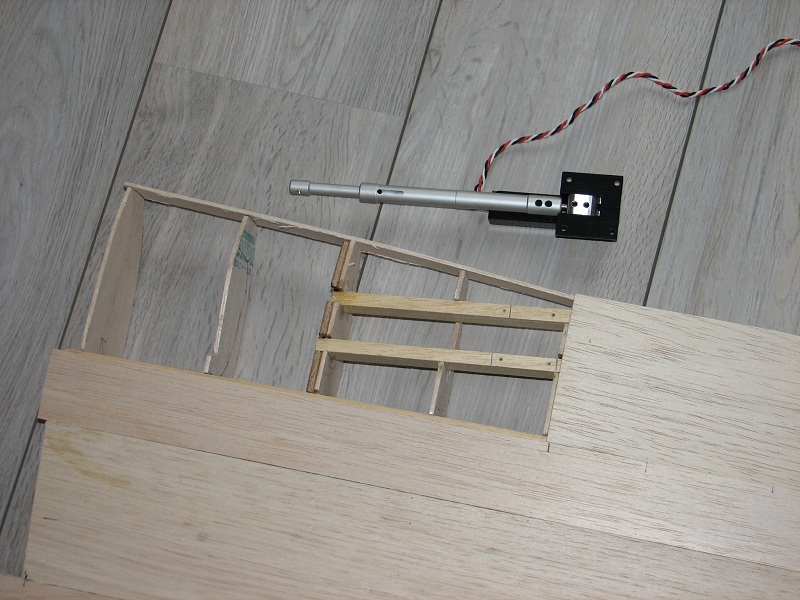
A notez que l'axe du train doit être raccourci à la Dremel de 3 mm pour bien reposer sur son support, ainsi que Stéphane me l'a précisé au téléphone.
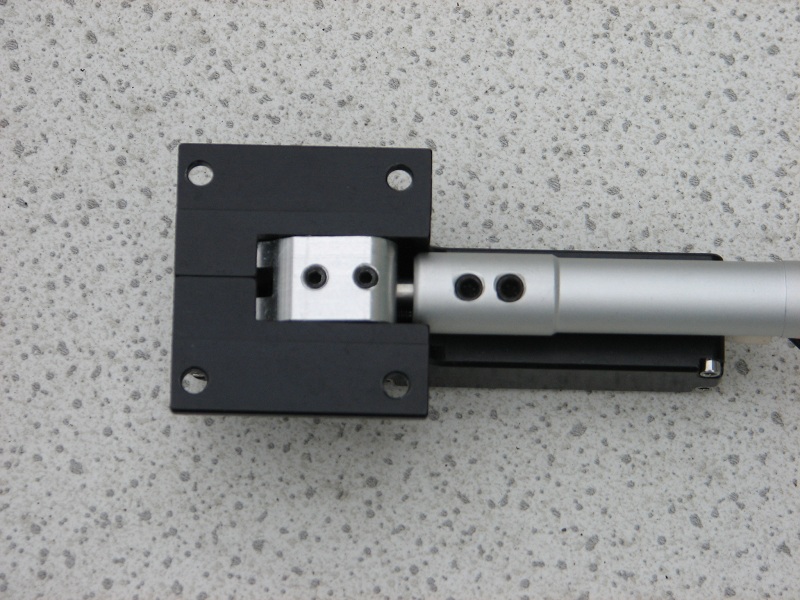
L'opération est simple : sortie de l'axe, découpe sur l'étau puis repositionnement.
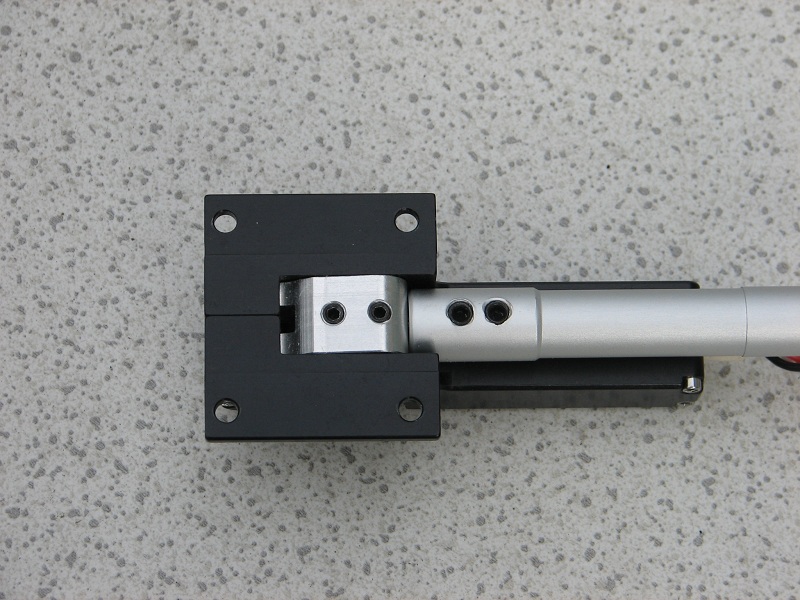
De cette façon, la jambe est en contact avec la partie en aluminium du train pour une meilleure répartition de l'effort.
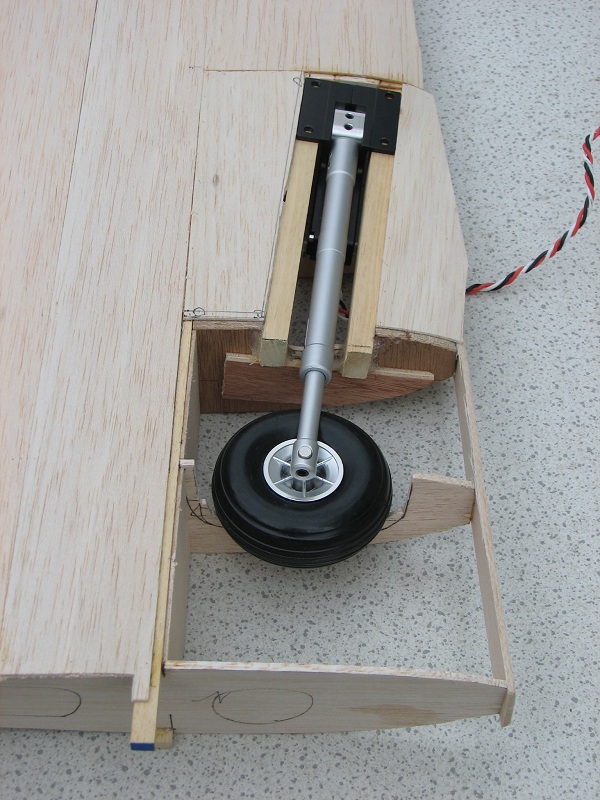
Par contre, l'orientation de la roue doit être correctement configurée train sorti : la photo explicative suivra.
Pour l'instant, je ne coffre pas l'extrado au niveau du puits de roue car il faut d'abord découper correctement la nervure n°2 pour laisser passer la roue.
Il ne faut pas oublier à ce stade de renforcer la nervure n°1 au bord d'attaque avec un bloc de balsa, qui sera destiné à accueillir le téton de centrage de l'aile : je le ferai plus tard. Donc ne pas oublier...
L'aile a été retournée : contrairement au plan qui prévoit de nombreux allègements sur les nervures, je les ai laissées pleines car le gain en masse est très faible si le balsa est bien choisi.
Par contre, j'ai fait les trous nécessaires au passage du câble du servo d'aileron.
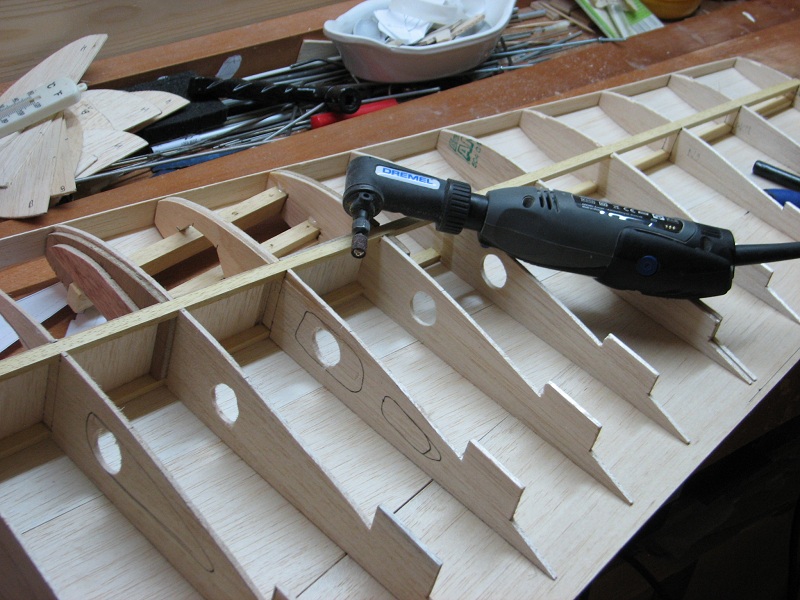
Un outil bien pratique. Qui a dit que Dremel était prothésiste dentaire ?
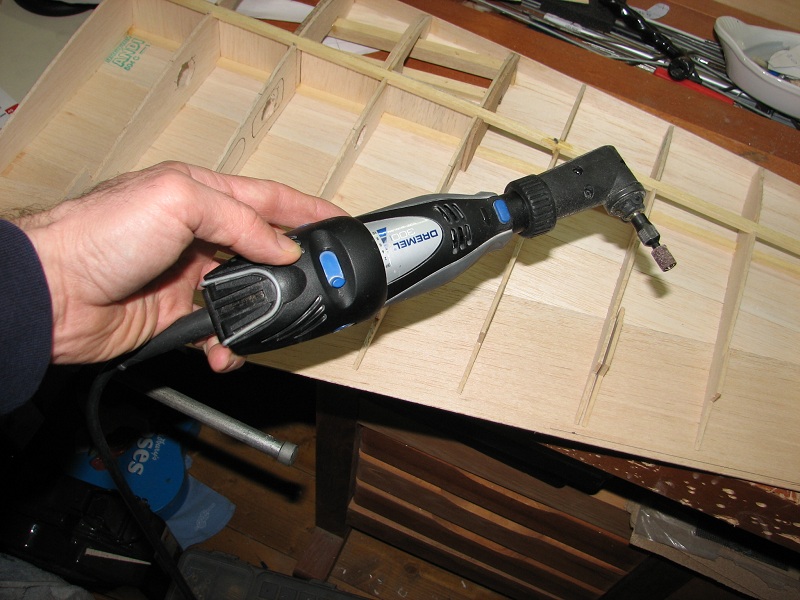
Les opérations se poursuivent avec le coffrage de l'extrados : côté bord d'attaque pour commencer. Le coffrage prend appui sur le longeron en samba, sur lequel j'ai tracé un trait au milieu afin que faire reposer 2 planches sur cette baguette.
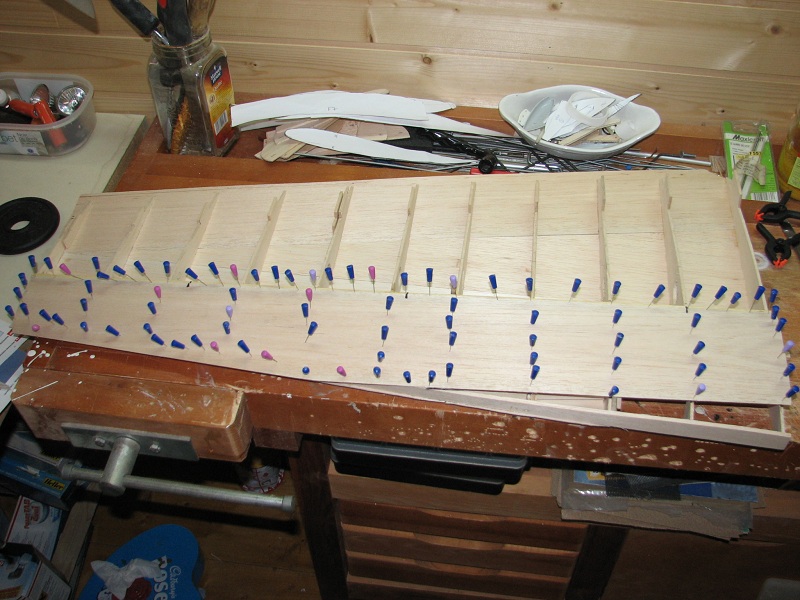
Le collage sec, j'ai tracé les dimensions de chaque aileron avant son coffrage. Je préfère cette méthode à celle du coffrage intégral de l'aile car elle me permet de préparer la découpe lorsque l'aile sera terminée.
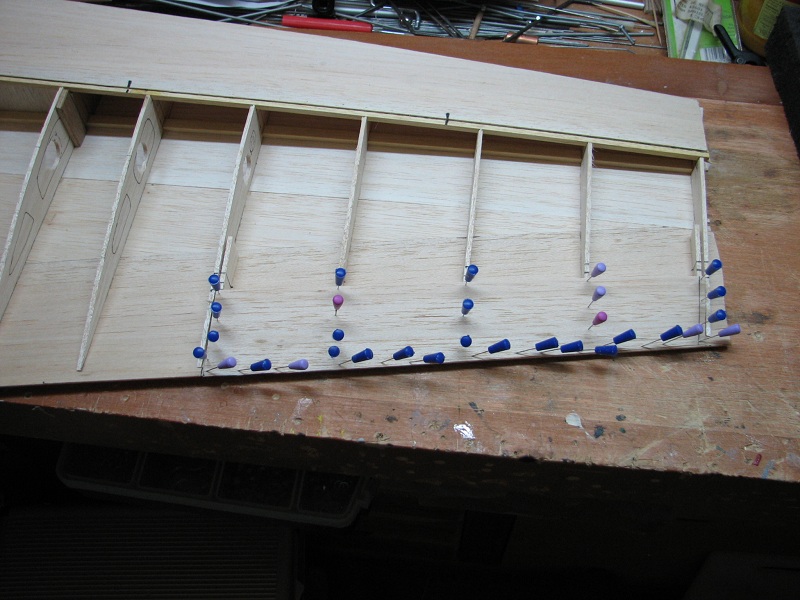
L'opération est plutôt simple : coffrage de l'extrados de l'aileron puis pose d'un longeron de renfort (non prévu sur le plan).
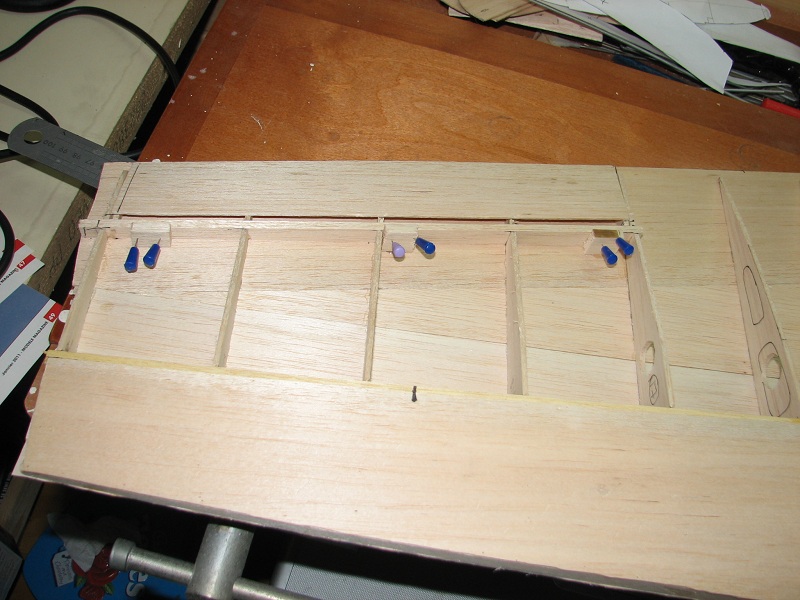
Ensuite, renfort avec quelques petits blocs de balsa en 50/10 pour recevoir les futures charnières en tissu.
Pour le renfort des vis de fixation des ailes, j'ai collé de la baguette triangulaire de bord de fuite.
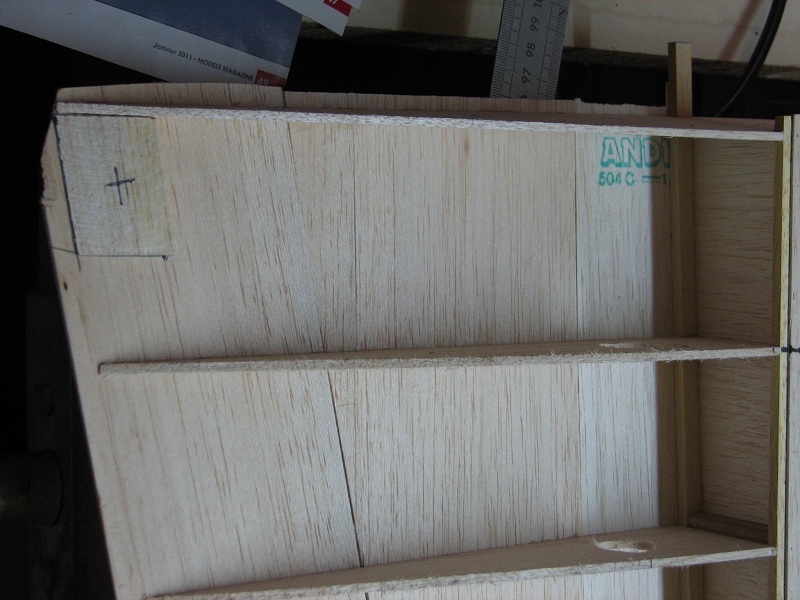
Le coffrage de l'aileron étant terminé, j'ai tracé l'axe de découpe à l'intrados, ainsi que l'emplacement de la trappe qui servira de support au servo d'aileron.
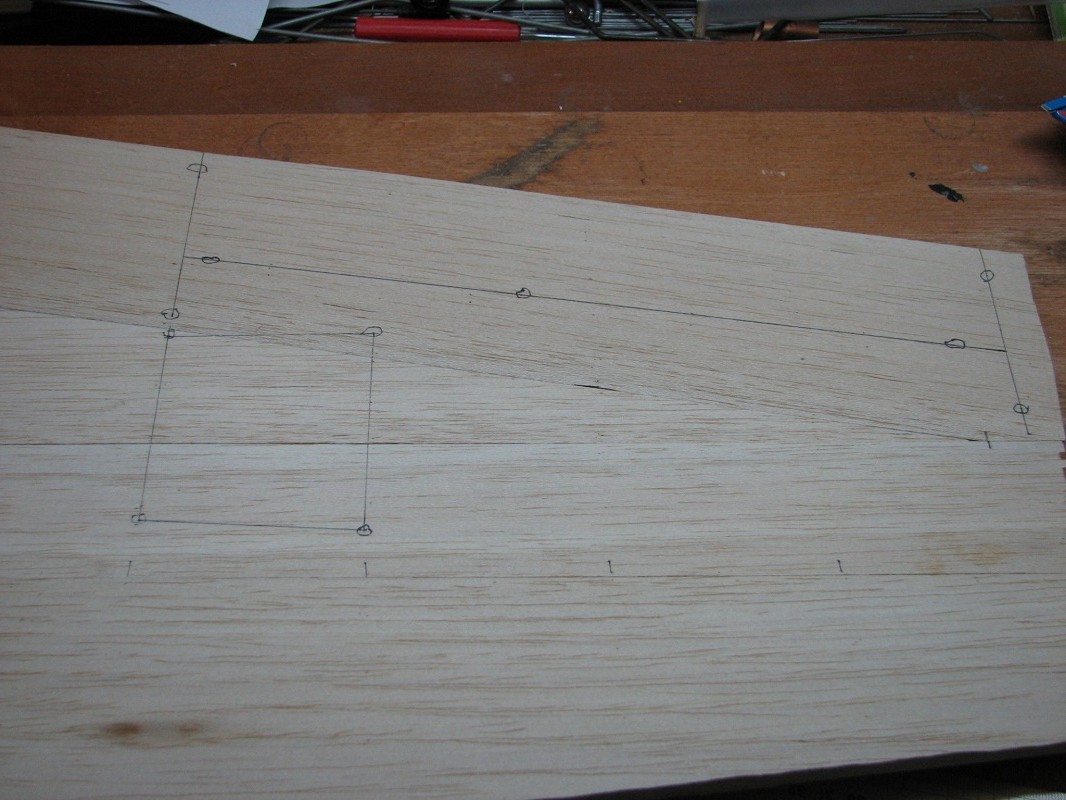
Le coffrage de l'extrados se poursuit sans difficulté : notez le fil pour le passage du câble du servo. Les rondelles sont d'un diamètre plus large que celui des trous, bien sûr...
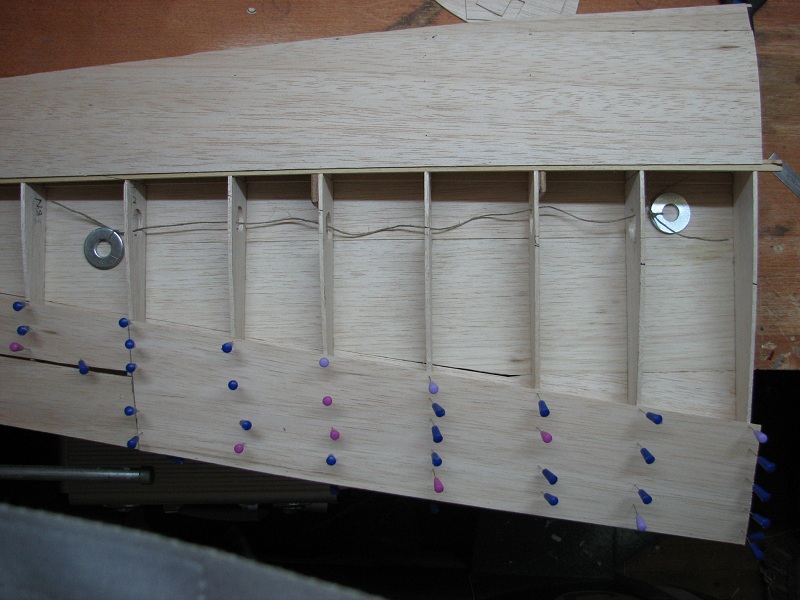
Une deuxième planche rejoint la précédente : le coffrage ne peut pas être terminé à cette étape de la construction car il est nécessaire d'entailler les quatre premières nervures pour faire coulisser la clé d'aile.
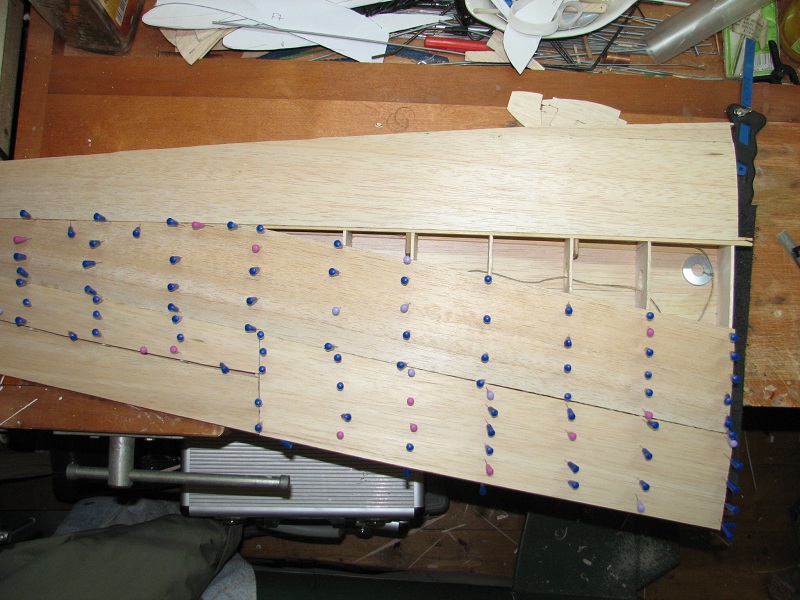
Lorsque les demi-ailes sont presque coffrées, il est nécessaire de poncer les planchettes au ras de la nervure d'emplanture et préparer la découpe des 3 premières nervures pour glisser la clé d'aile.
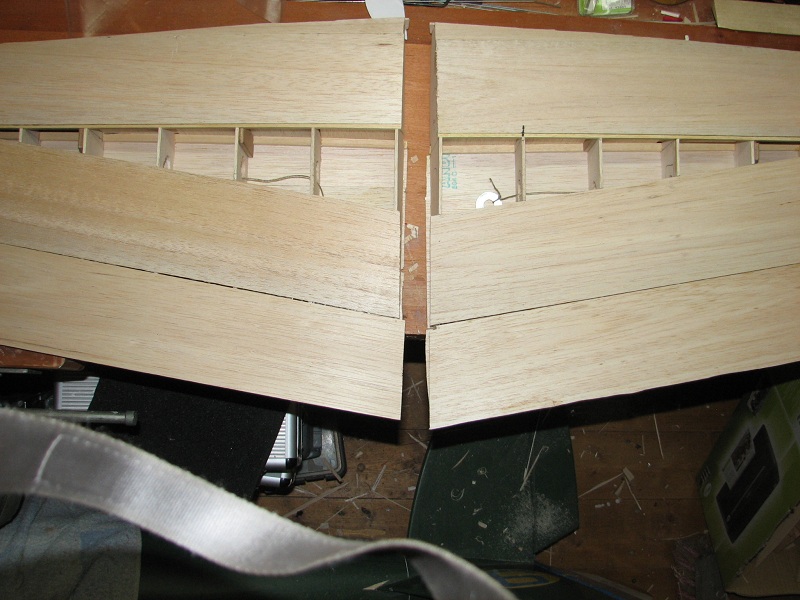
Une lame de scie à métaux permet de découper presque proprement les 5 mm d'espace requis.
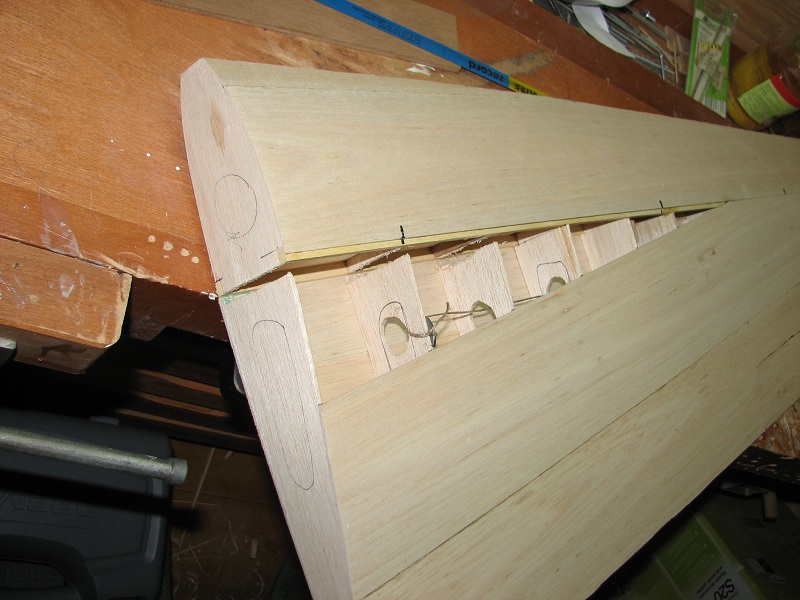
Quant à la clé, j'utilise exclusivement du CTP bon marché de 5 mm trouvé chez mon détaillant en bricolage : l'expérience démontre que cette qualité est largement suffisante pour notre loisir, étant entendu que cette clé mesure pas loin de 50 cm.
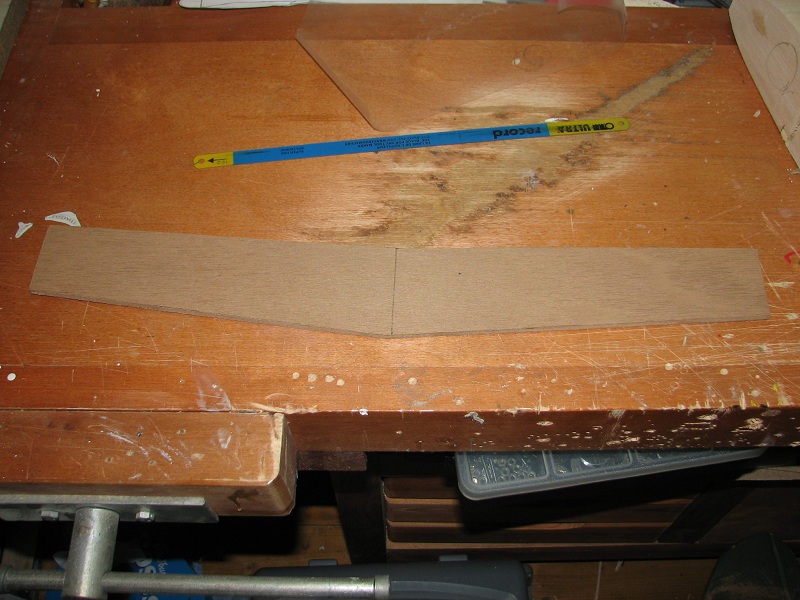
Collé à l'epoxy sur les longerons en samba, la résistance mécanique est très convaincante.
J'ai commis une grossière erreur : la nervure d'emplanture était calée à 7 ° sur le chantier alors que ma clé a été découpée dans la précipitation à 5 °...
Le montage à blanc a révélé cette erreur par un écart très significatif entre les deux nervures d'emplanture : presque 8mm  au niveau de la clé.
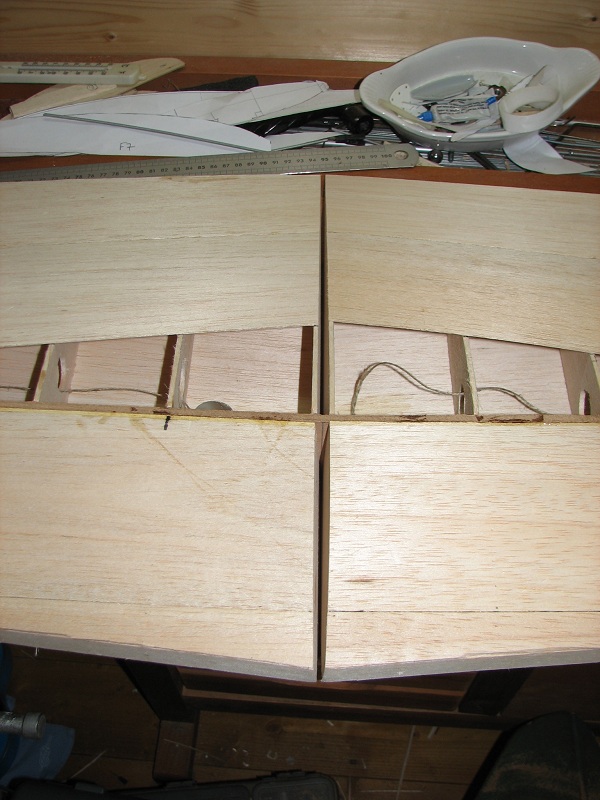
Ne souhaitant pas redécouper une clé supplémentaire, j'ai procédé à son collage et combler le vide avec des chutes de balsa poncées en biais.
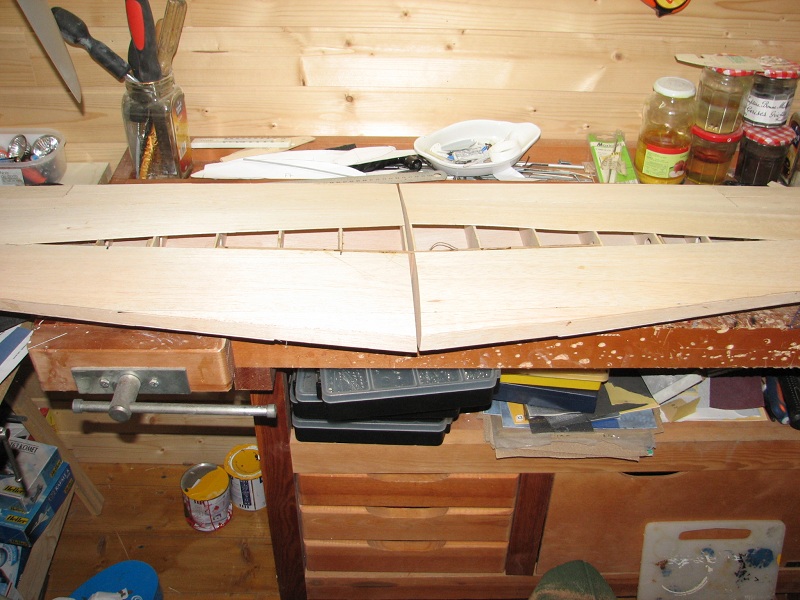
A ce moment de la construction, je n'avais pas pensé un seul instant que les roues ne seraient plus perpendiculaires au sol lors de leur sortie...
Je croise les doigts car je n'ai pas encore vérifié.
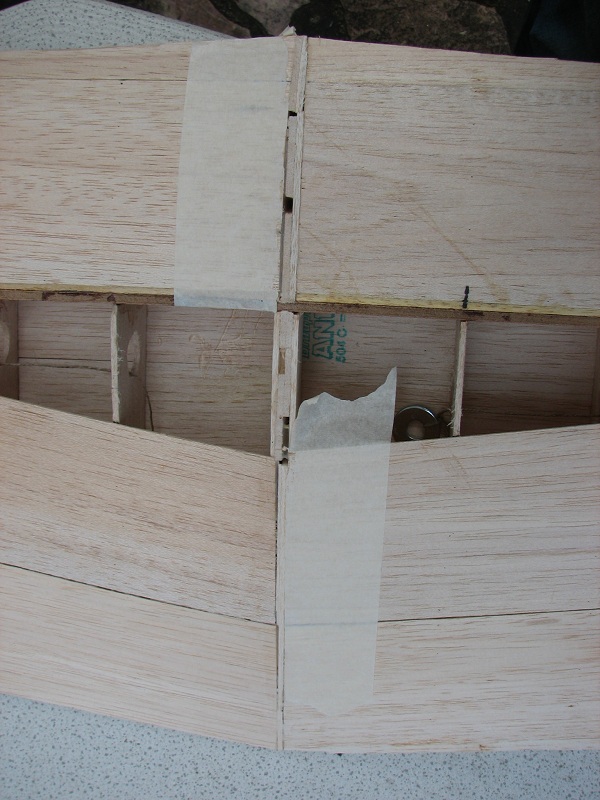
Pour poncer les chutes, compte tenu du dièdre de l'aile, j'utilise une bande du tyro de masquage pour protéger la partie de l'aile.
Le ponçage intégral de la voilure efface toutes les imperfections au niveau du raccord entre les planches.
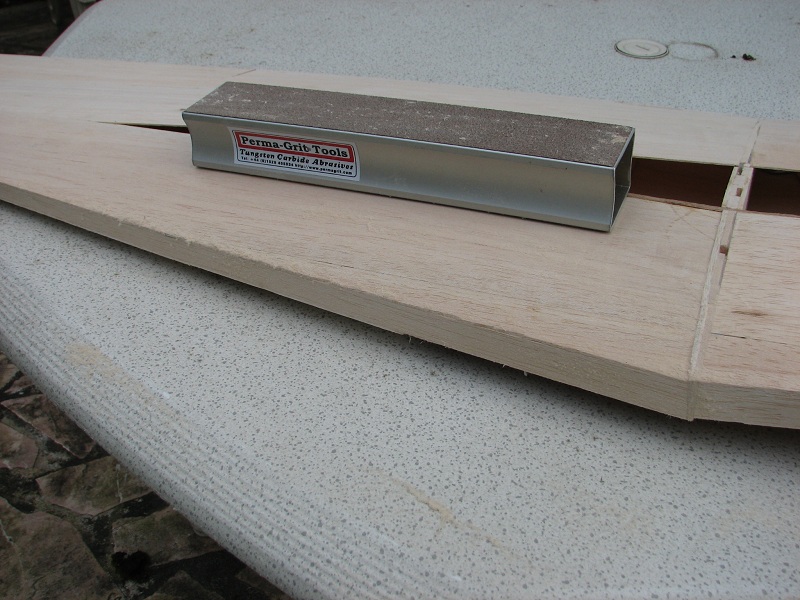
Je n'ai pas pu résister à un montage à blanc.
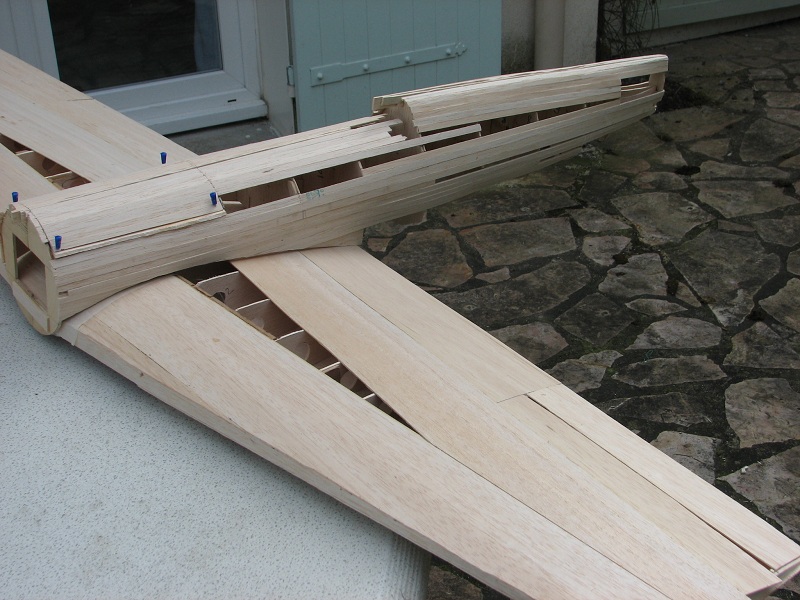
Donc retour sur l'aile : les raccords entre les planches de coffrage en balsa 15/10 ont été comblés avec un enduit de finition Polyfilla, appliqué avec une carte en plastique. Le temps de séchage est rapide, à peine 1 heure.
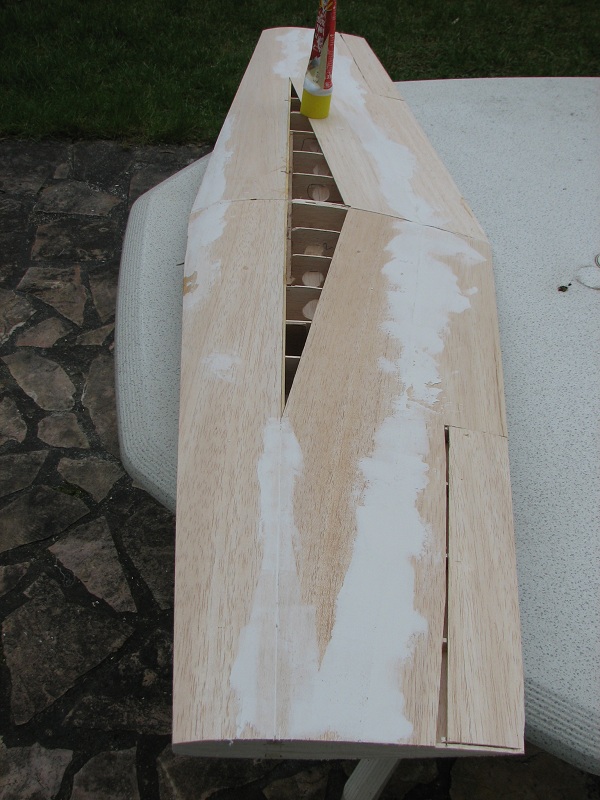
Cet enduit est très léger et se ponce sans aucune difficulté.
J'utilise une petite cale souple et le tour est joué en 5 min : il suffit ensuite de bien dépoussiérer avec une éponge légèrement humide; plusieurs passages étant nécessaires.
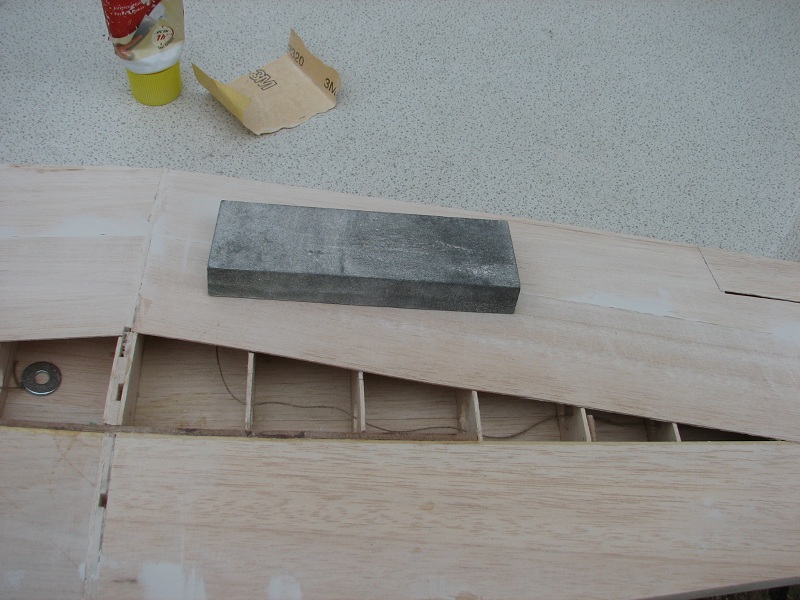
Il ne reste pratiquement plus de matière et les les irrégularités sont toutes corrigées.
La construction se poursuit avec le collage des bords d'attaque en balsa 50/10, que je choisis un peu dur.
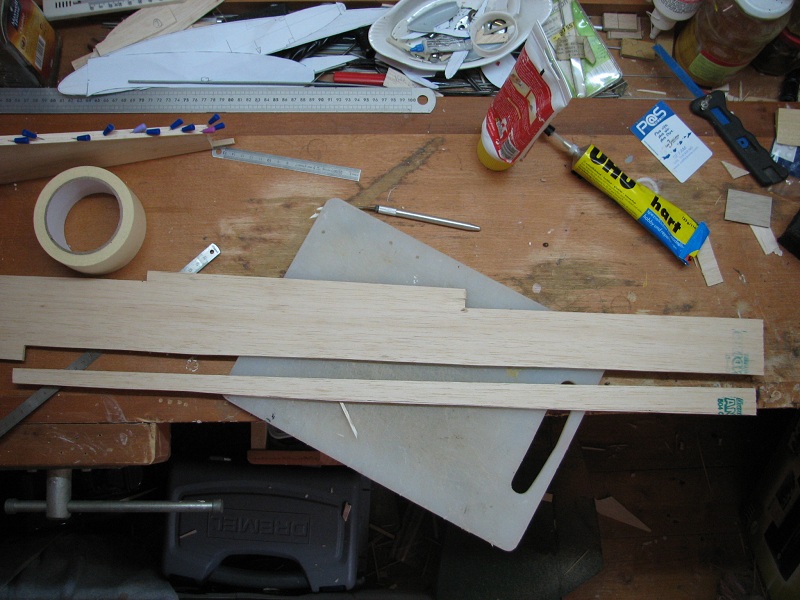
Pour assurer une bonne pression, j'utilise des épingles insérées en biais dans le balsa : effet garanti :wink:
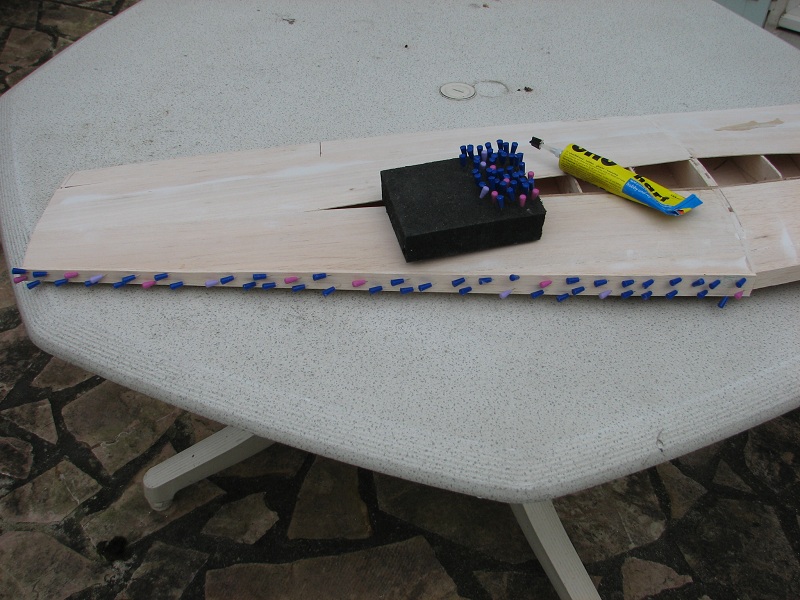
Lorsque la colle est sèche, intervention du rabot pour une finition grossière.
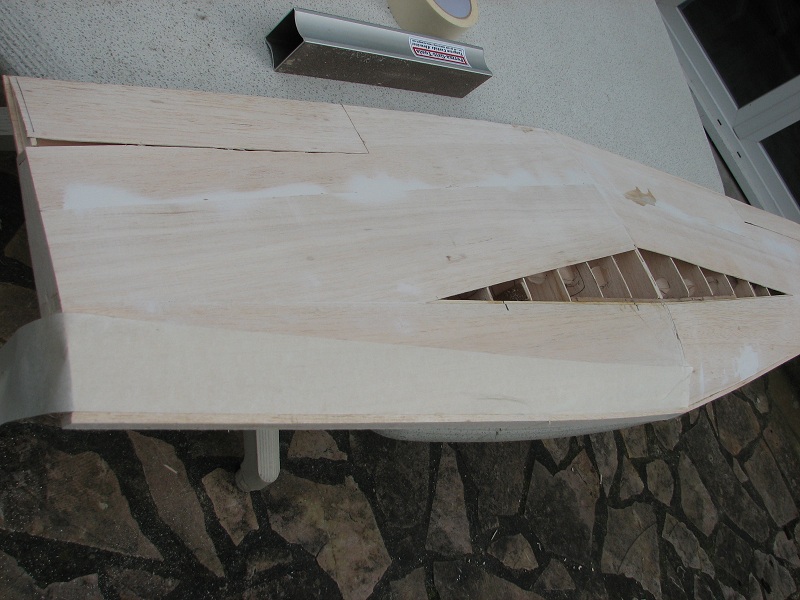
Pour un ponçageÂ
précis, le coffrage du bord d'attaque est protégé avec du scotch de masquage : quand la cale à poncer effleure le tissu, il suffit de le retirer et de finir tout doucement. Avec cette méthode, le coffrage n'est pas fragilisé.
L'opération sur l'aile se poursuit avec la mise en place du téton de centrage, nécessaire pour la mise en croix.
Compte tenu de la flèche de l'aile, j'ai collé des renforts au niveau du bord d'attaque ainsi qu'une petite clé en CTP de 5 mm.
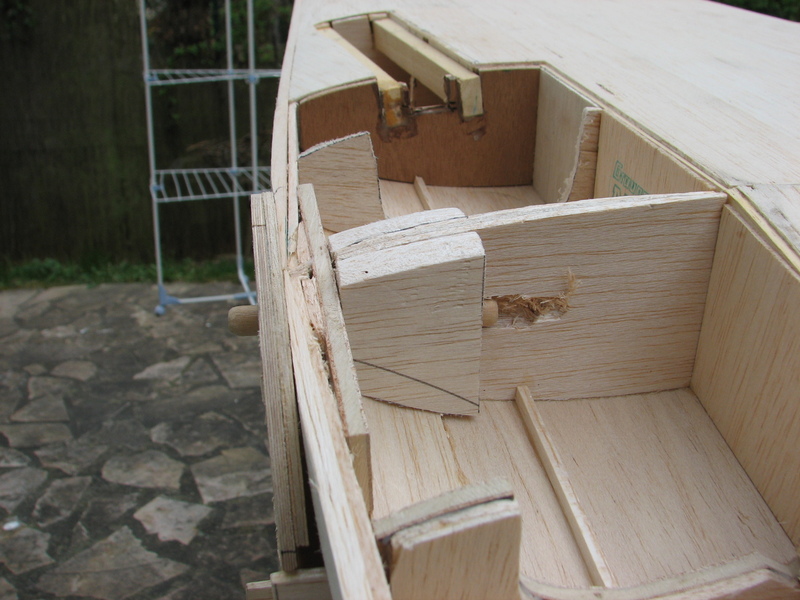
A noter que le couple du fuselage (réalisé en deux morceaux du fait de l'assemblage en demi-coquilles) a été renforcé par un autre couple (non coupé celui-la) et percé en son centre au bon diamètre.
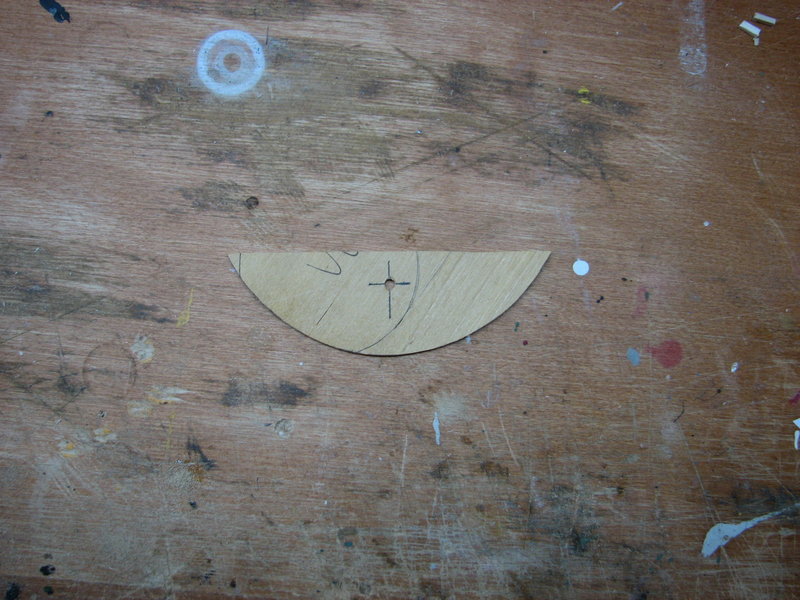
PourÂ
préparer la triangulation avec le fuselage, il est nécessaire de découper l'assise des karmans mais aussi de positionner les vis de fixation de l'aile.
Les longerons d'assise du fuselage sont renforcés avec du CTP de 3 mm au niveau de l'encoche de la plaque destinée à recevoir les écrous à griffe.
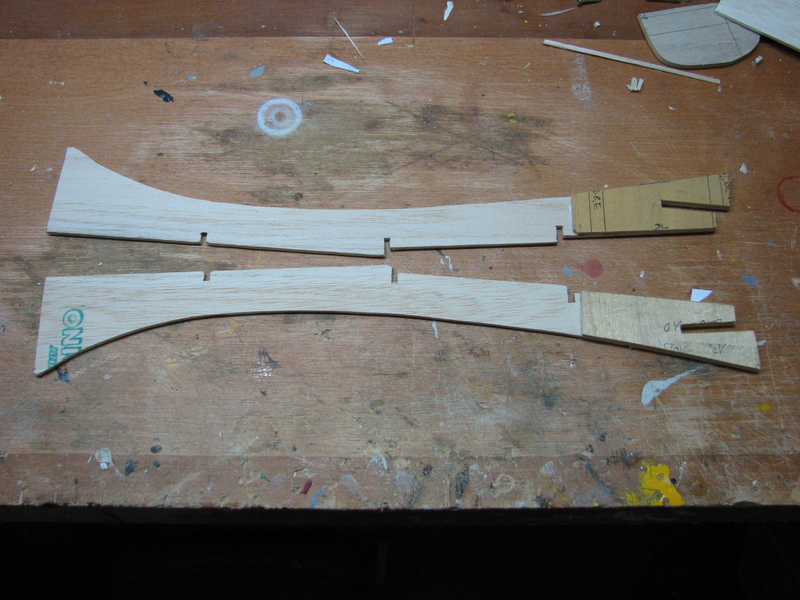
Ceux-ci sont insérés dans une plaque de CTP de 5 mm, la colle epoxy étant appliquée uniquement sur la partie plate des écrous pour éviter des coulures dans le pas de vis.
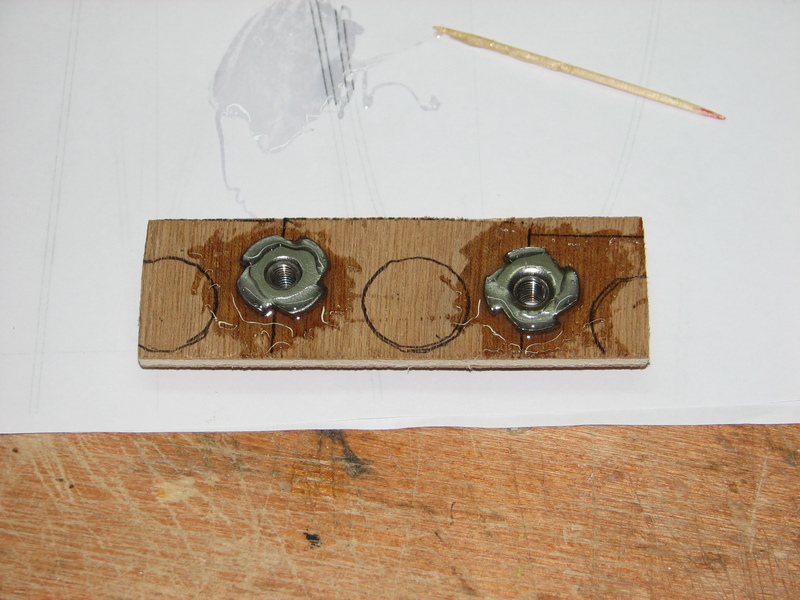
Pour de l'aile, la base des karmans est réalisée en balsa de 1,5 mm.
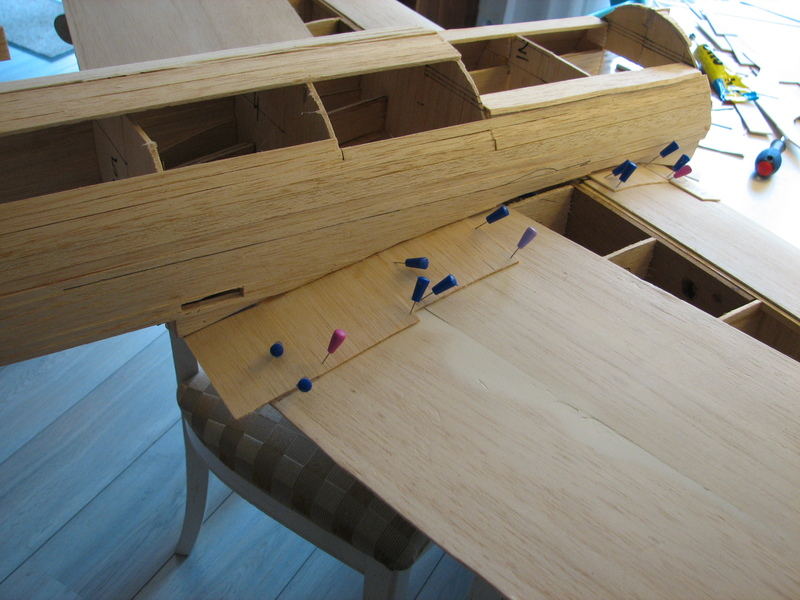
La triangulation peut donc être vérifiée, suivie du perçage de l'aile.
L'étape suivante concerne la construction du pied de dérive.
J'ai oublié de prendre des photos, mea culpa.
Il est très simple et le résultat final est assez sympa (le coffrage est en 15/10).
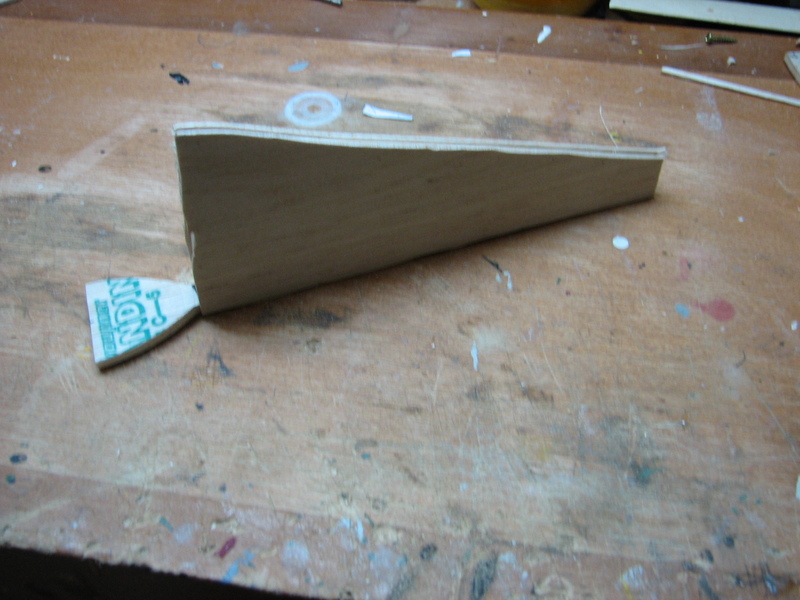
Pour le volet mobile, Laurent Buyssine avaitÂ
prévu un morceau de balsa plein découpé à la forme adéquate. Cependant, afin d'éviter le plombage du nez, j'aiÂ
préféré réaliser le volet en structure. Des rectangles de balsa sont collés sur une âme en 15/10, lesquels seront ensuite poncés à la forme souhaitée. Le gain en masse n'a pas été vérifié, mais il ne faut pas oublier que 5 grammes gagnés à l'arrière permet d'éviter au moins 4 fois plus de plomb devant.
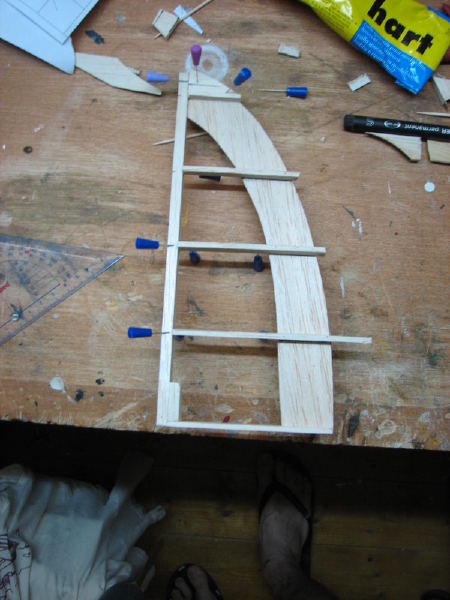
Il me reste à finir le coffrage de l'aile et la pose des karmans.
Sur ce point, la méthodeÂ
prévue est assez simpliste : le plan ne contient aucun profil des triangles de positionnement, seuls étant dessinés les formes supérieures et inférieures.
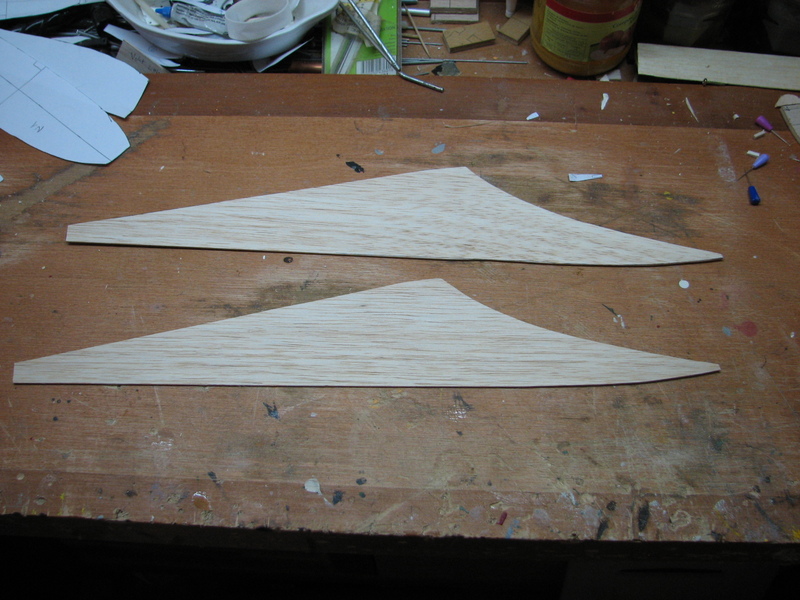
De même, le contour des karmans sur le fuselage ne figure nulle part : c'est une opération casse-tête et j'ai laissé l'aile en l'état pour avancer sur le capot moteur.
Le planÂ
prévoit un capot moteur réalisé entièrement en balsa : blocs pour l'arrondi et lamelles de 15/10 pour la partie arrière.
Ayant trouvé que la partie arrondie était trop prononcée par rapport aux photos de la réplique grandeur, j'ai modifié la forme finale.
Une réalisation à base de polystyrène extrudé aurait sans doute été plus simple mais j'ai tenté le balsa.
Le capot a été réalisé en 2 demi-coquilles.
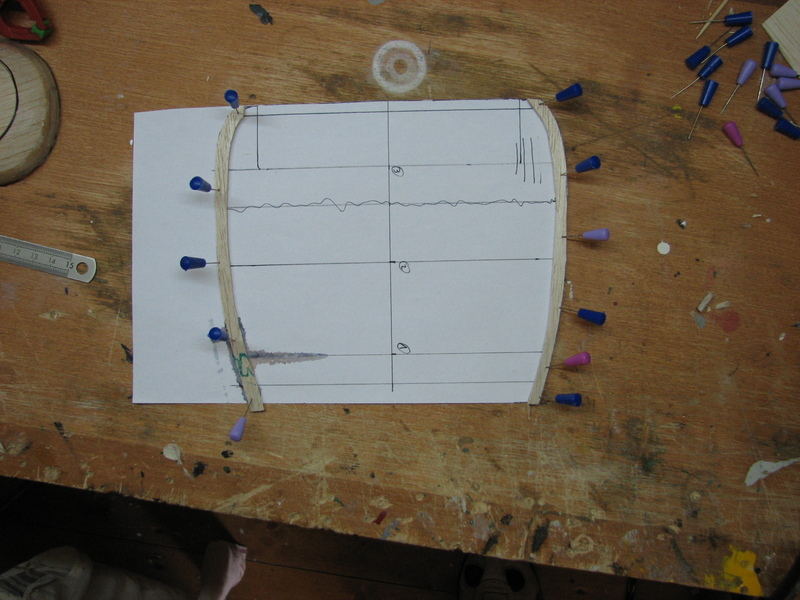
Souhaitant installer un faux moteur en étoile, je me suis inspiré de la méthode de Roger Nieto (pour les petits nouveaux, il s'agit du pape français de la maquette, non avare en conseils).
Il faut réaliser des faux-couples intermédiaires pour rigidifier la structure et un troisième couple composé de 7 branches qui supporteront les faux cylindres (7 cylindres apparents car le grandeur avait 14 cylindres en deux rangées de 7).
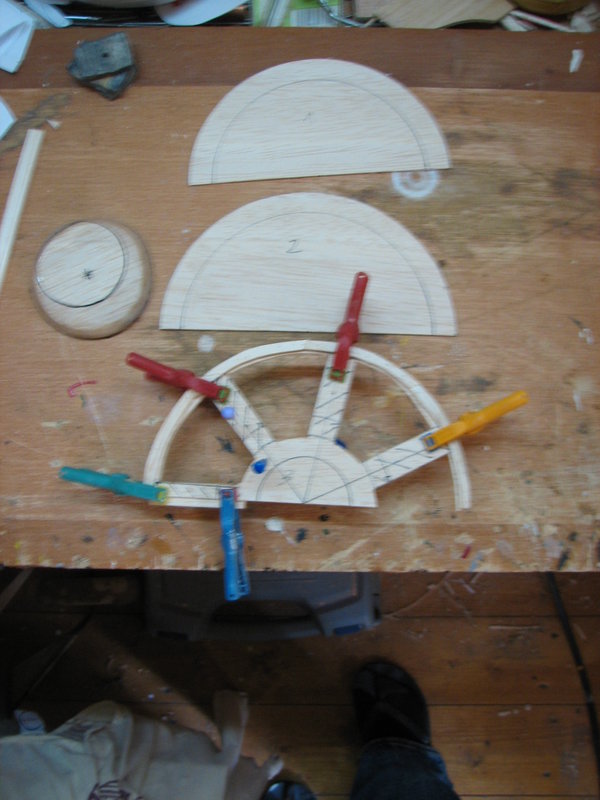
Chaque branche est renforcée avec du balsa en fibre inversée.
Ensuite le coffrage commence en lattes de balsa 15/10. J'aurai du le faire en 30/10 afin de garder de la marge pour le ponçage.
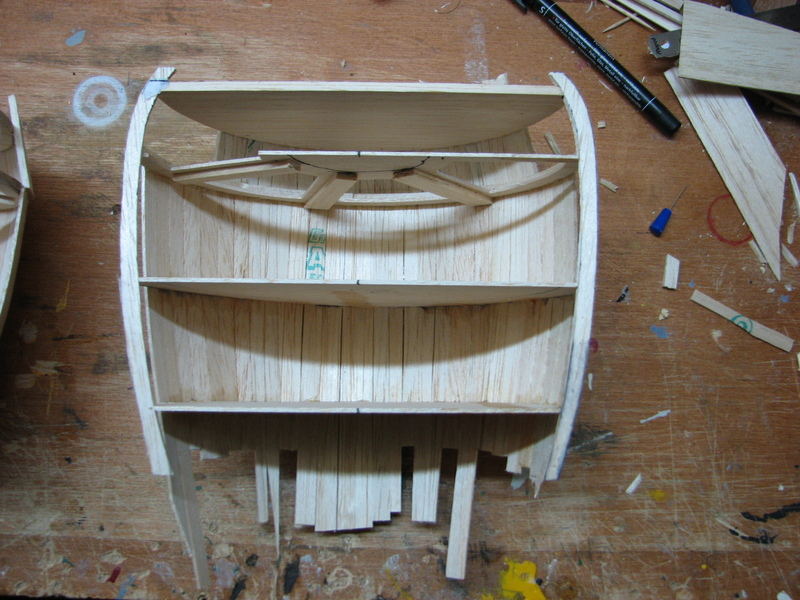
Puis les 2 morceaux :
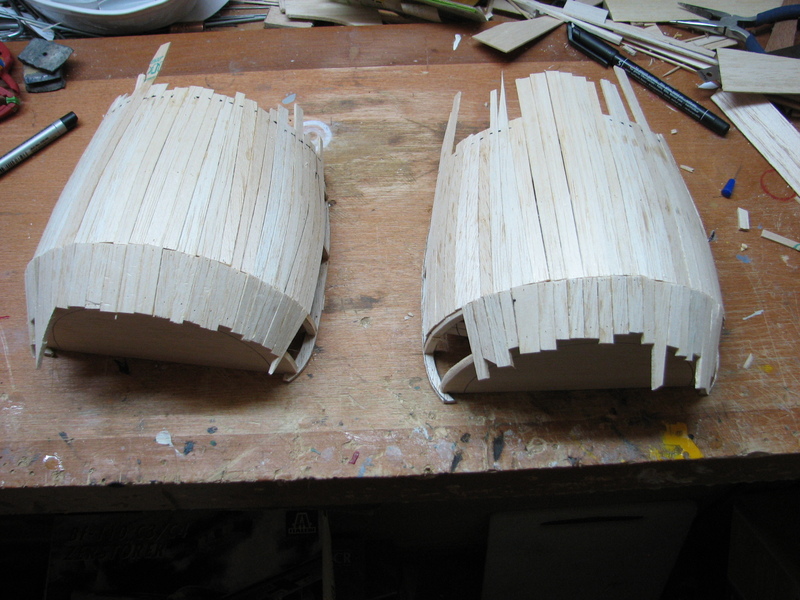
L'arrondi semble non-arrondi : c'est normal, il sera obtenu par ponçage.
Les deux parties sont ensuite collées : vous noterez que le coffrage n'était pas entièrement terminé afin de laisser de la place au pinces de serrage.
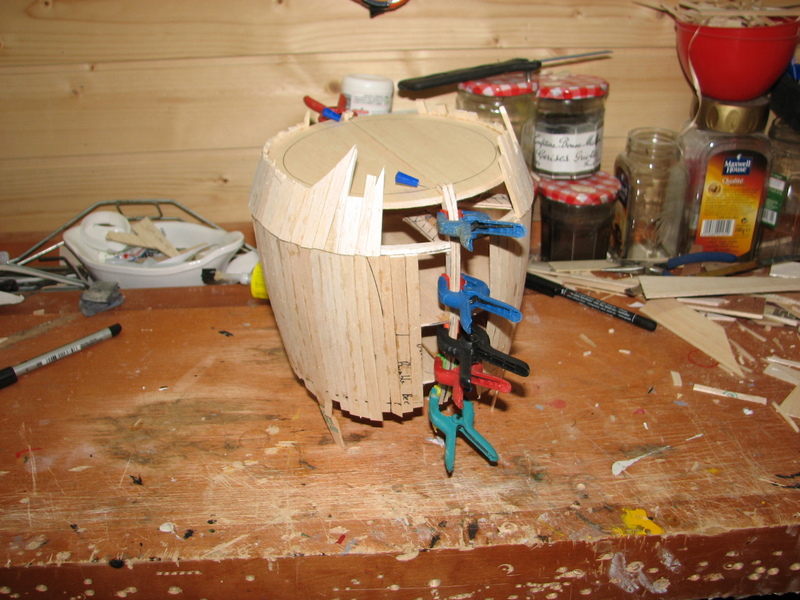
Pour le faux-moteur, le carter a été réalisé après découpe d'une bouteille de soda : il ne sera pas maquette, honte à moi.
Le problème c'est que la partie avant d'un brushless est beaucoup plus large que l'arbre d'un moteur thermique.
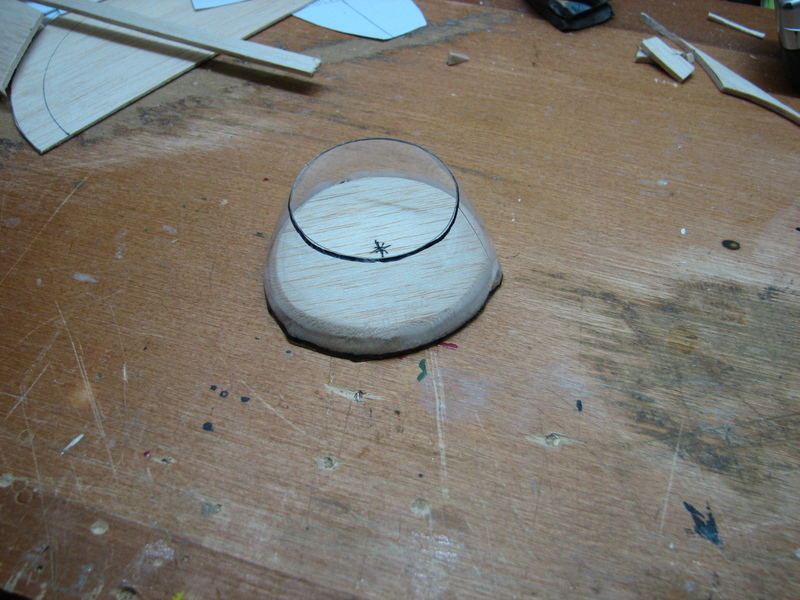
Il est assez simple à construire : une plaque de balsa sert de support de collage sur le couple interne du capot. Le carter est donc collé dessus après ébavurage du plastique et réalisation de petits trous pour que l'epoxy puisse accrocher correctement.
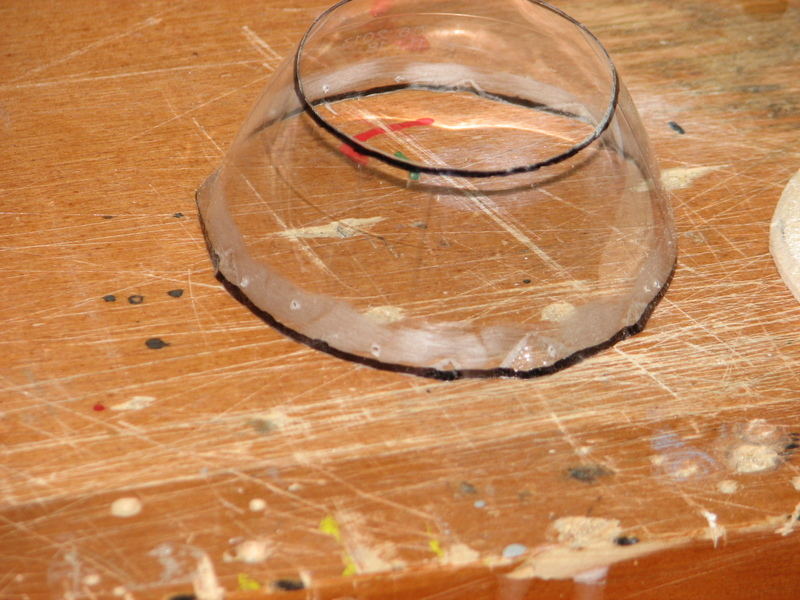
Côté pile : il faudra travailler un peu la finition... Les lignes de découpe sont déjà dessinées afin de creuser proprement à la Dremel.
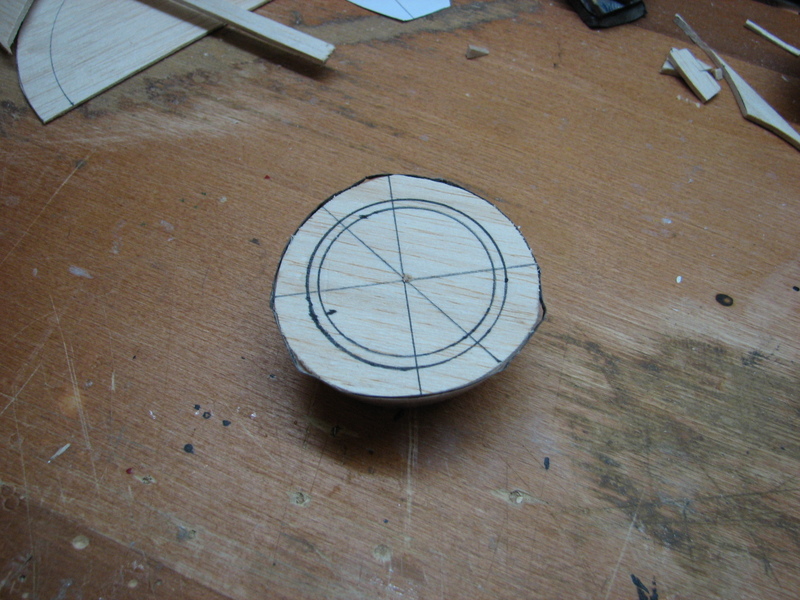
Voilà le moteur. Epower 4130-400 : il s'agit d'une copie des moteurs Axi que j'utilise depuis plus de 4 ans (les vols s'accumulent sans aucun souci). Le KV de 390 permet de tirer en 6 S une APC 16x10 sous 1.000 Watts ce qui est largement suffisant pour se faire plaisir avec une maquette de warbird ou ce futur Hughes jusqu'à 4,5 Kg.
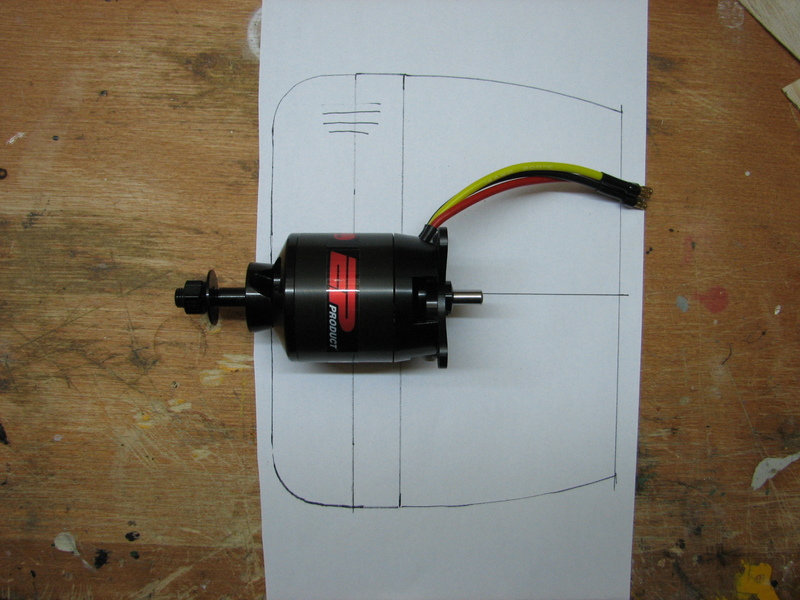
J'ai pas mal avancé sur le capot moteur.
Lorsque le coffrage est entièrement terminé, j'ai découpé la flasque avant et miracle, le support du faux moteur en étoile apparaît ...
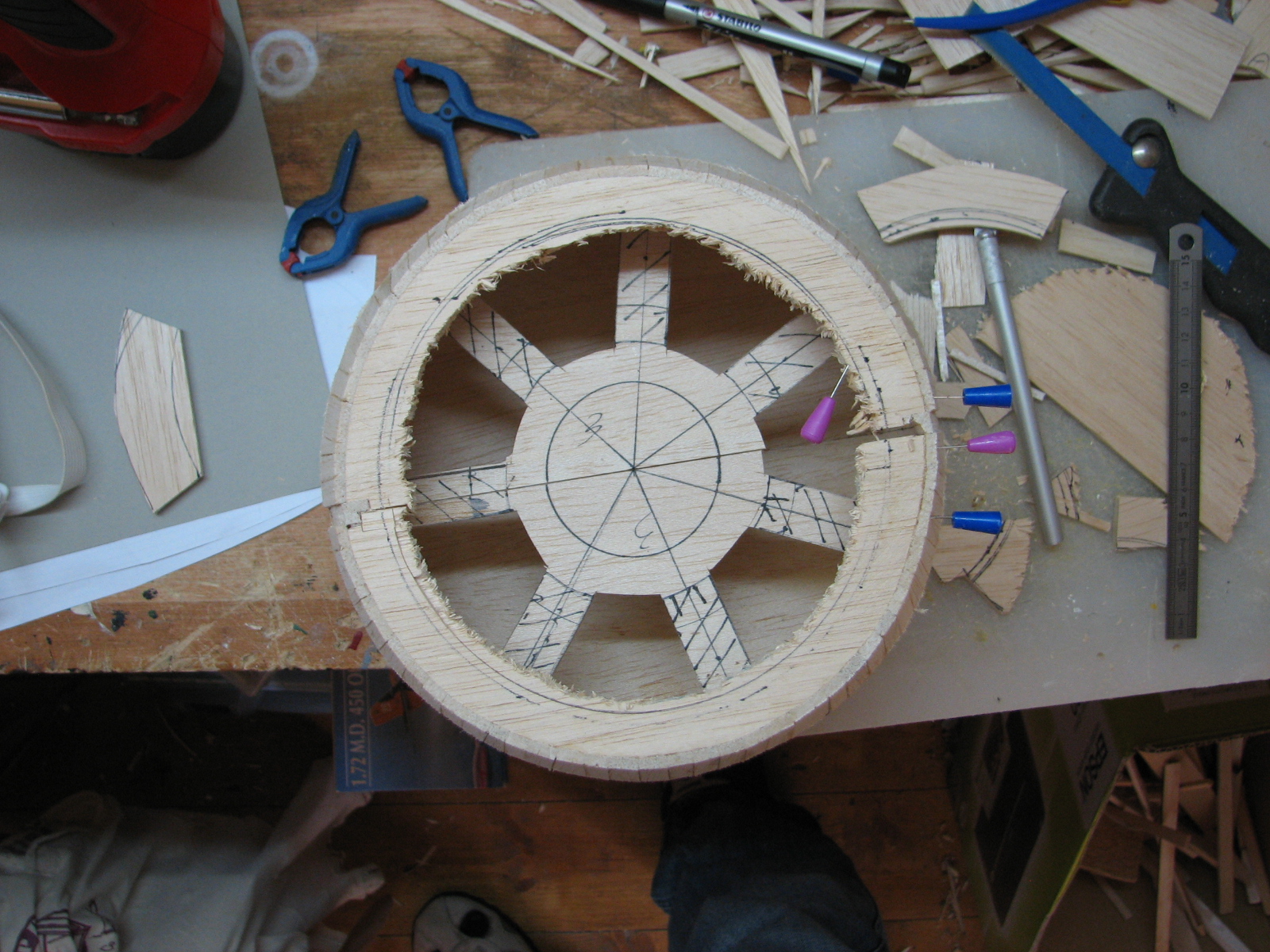
J'ai collé une nouvelle épaisseur de 4 mm afin de réaliser l'arrondi du capot par ponçage.
Le résultat final est satisfaisant à défaut d'être excellent : le ponçage n'étant pas uniforme, on remarque quelques irrégularités en vue de face. La prochaine fois, je ferai un gabarit pour m'aider dans le ponçage.
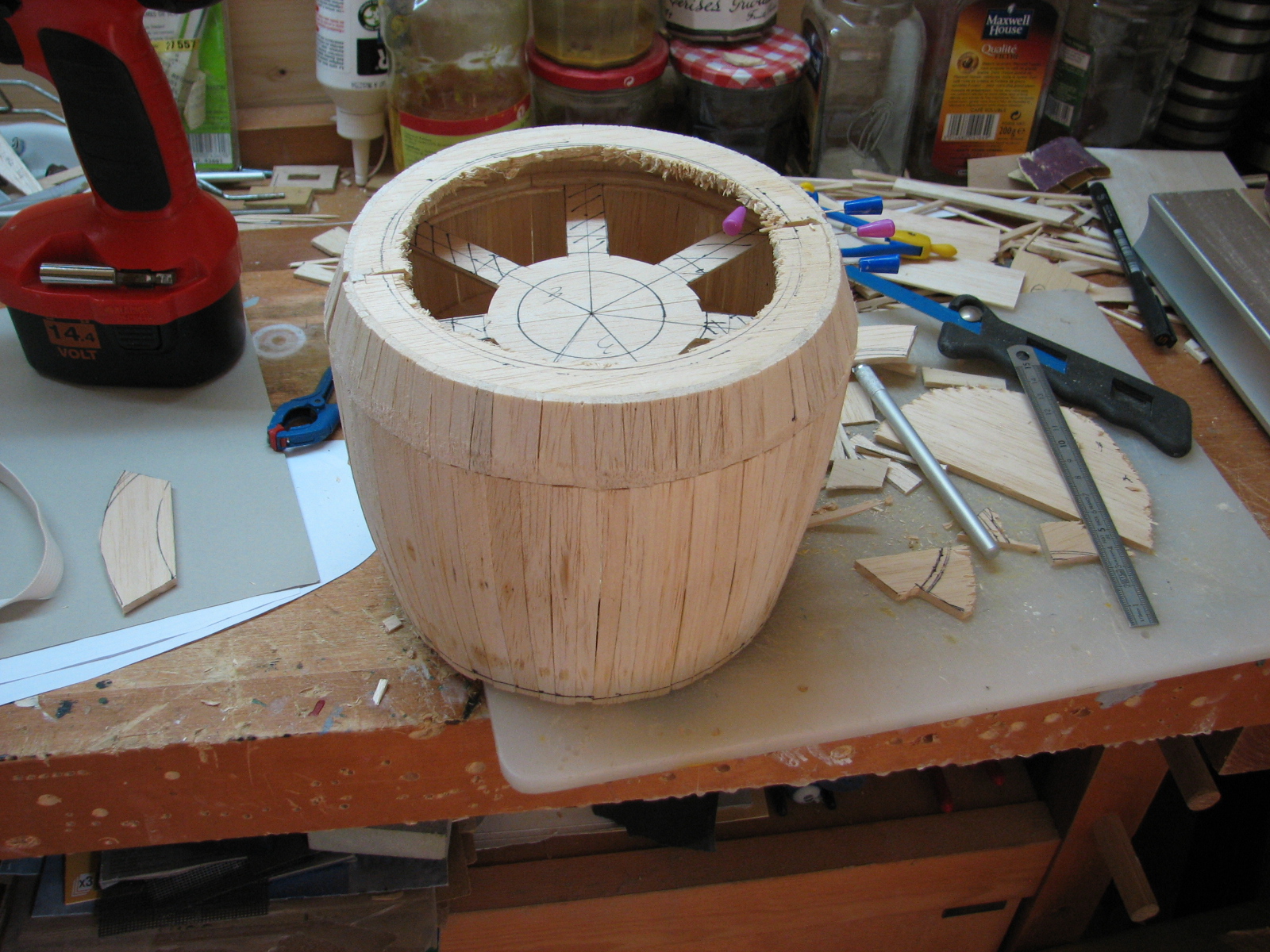
J'ai posé à blanc le carter du moteur sur les branches des cylindres : l'effet visuel est plutôt s
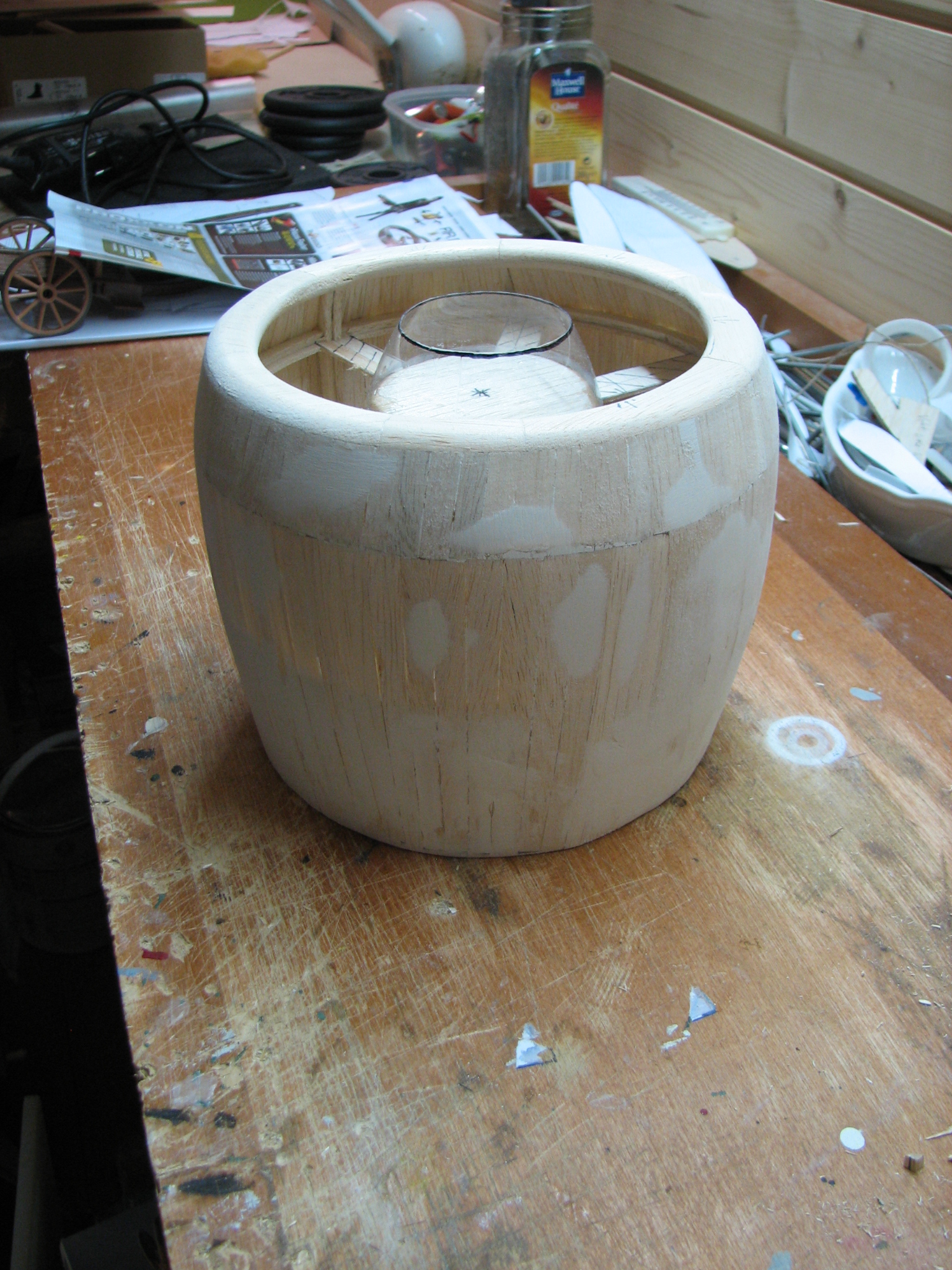
Il me reste à découper des carrés de CTP de 0,4 mm et de balsa de 1,5 mm pour réaliser les ailettes des cylindres.
A présent, retour sur le fuselage et les karmans.
La méthode prévue par Laurent Buissyne est faisable à condition de choisir du bois bien souple.
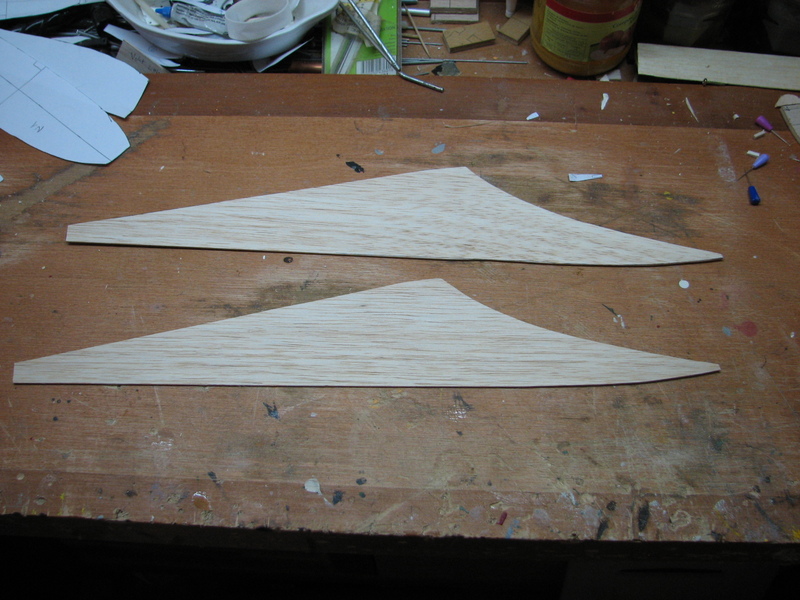
Compte tenu de la longueur de ces karmans, autant vous dire que ce n'est pas facile...
J'ai abandonné cette technique pour retenir la méthode classique.
Il faut donc découper des triangles de balsa légèrement incurvés.
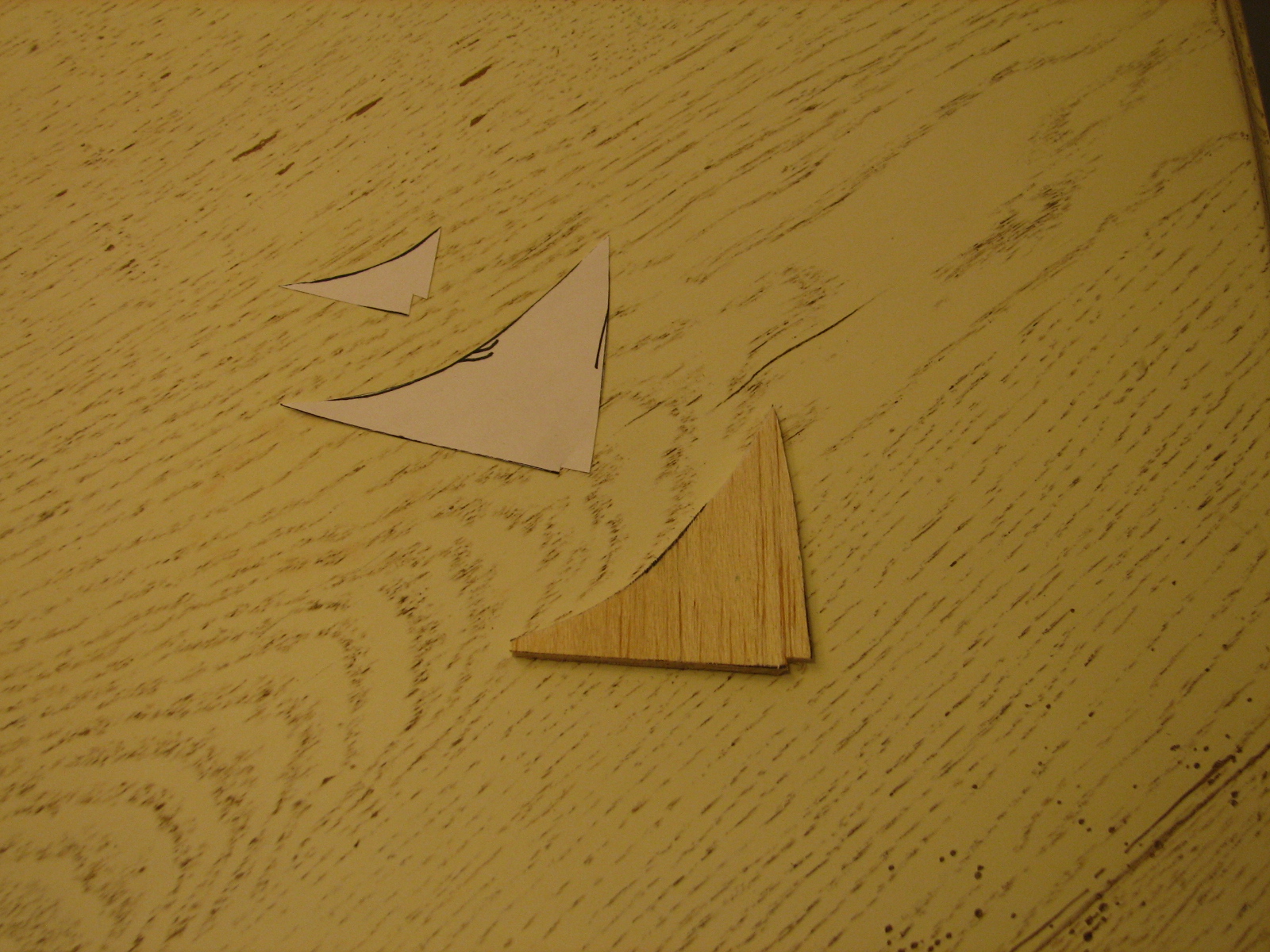
Pour cette opération, l'aile est fixée sur le fuselage et les triangles sont collés sur l'assise et le fuselage. La pose des lattes commence en suivants les contours dessinés sur le fuselage.
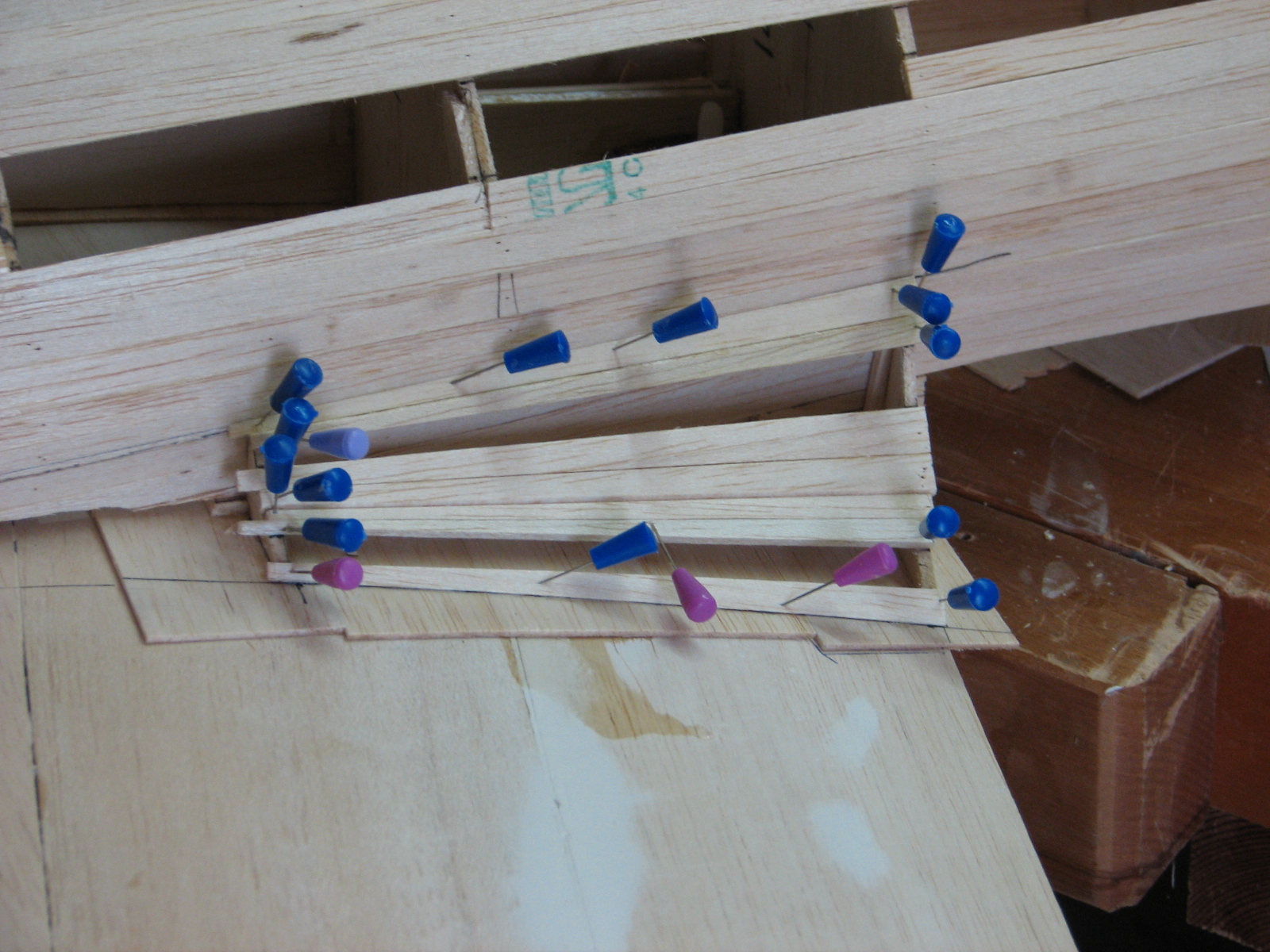
Il faut au moins une bonne heure de chaque côté, sans compter le temps de séchage : c'est long mais beau.
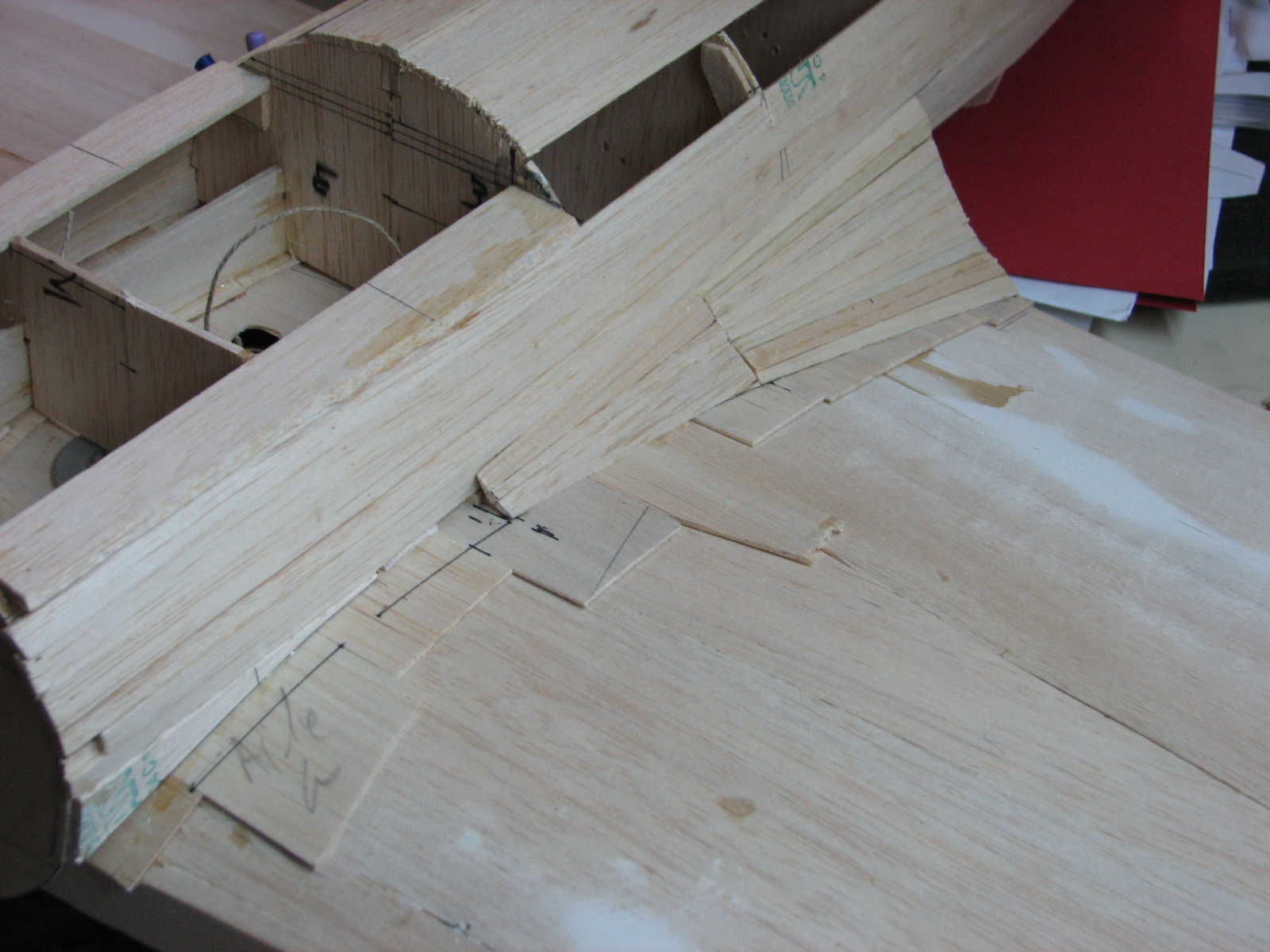
Pour la partie avant, les karmans sont construits avec des morceaux de balsa poncés à la forme qui va bien.
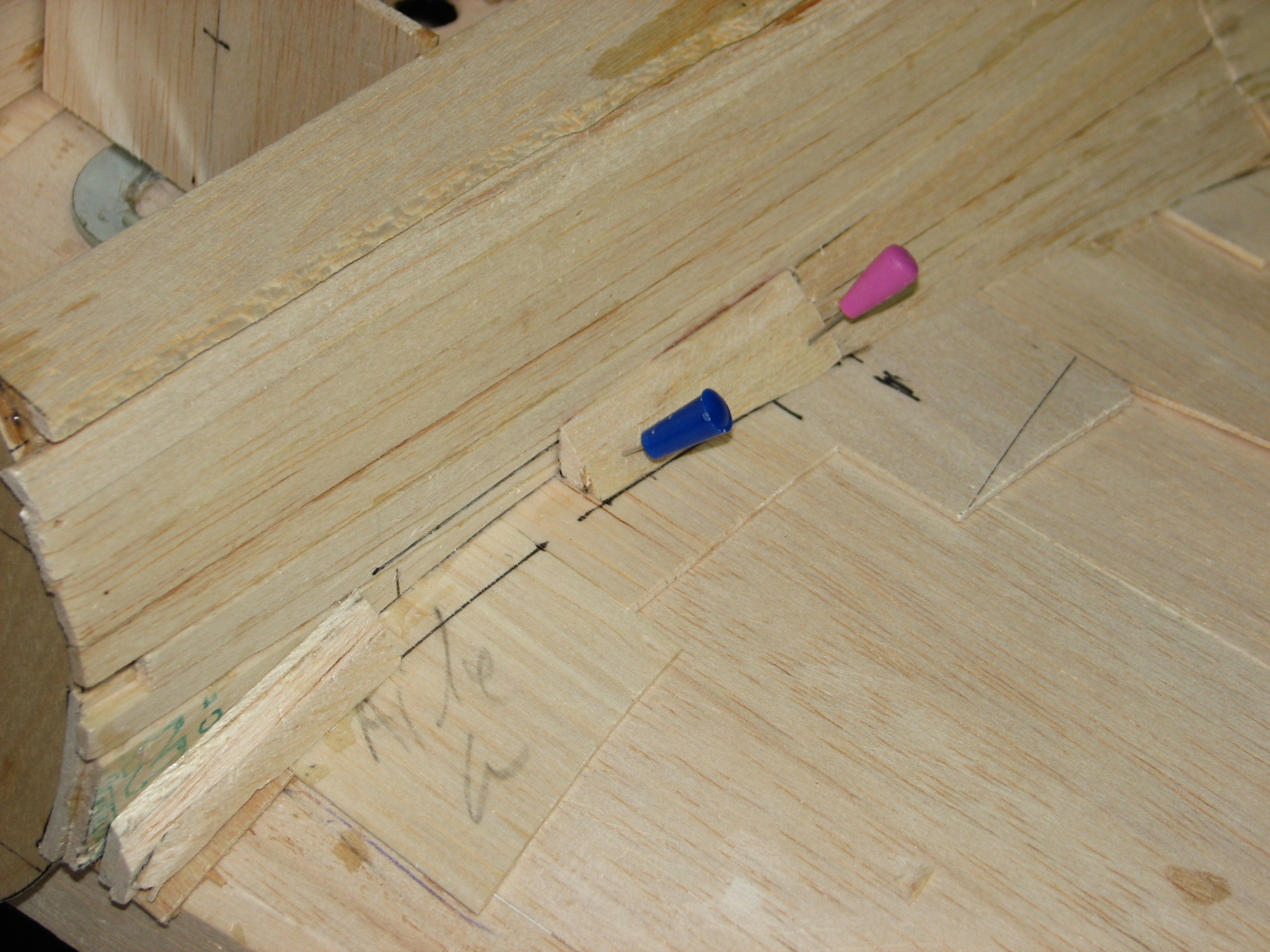
Pour l'instant, l'assise n'est pas encore découpée correctement et il reste à poncer aux formes les plus proches de la réalité.
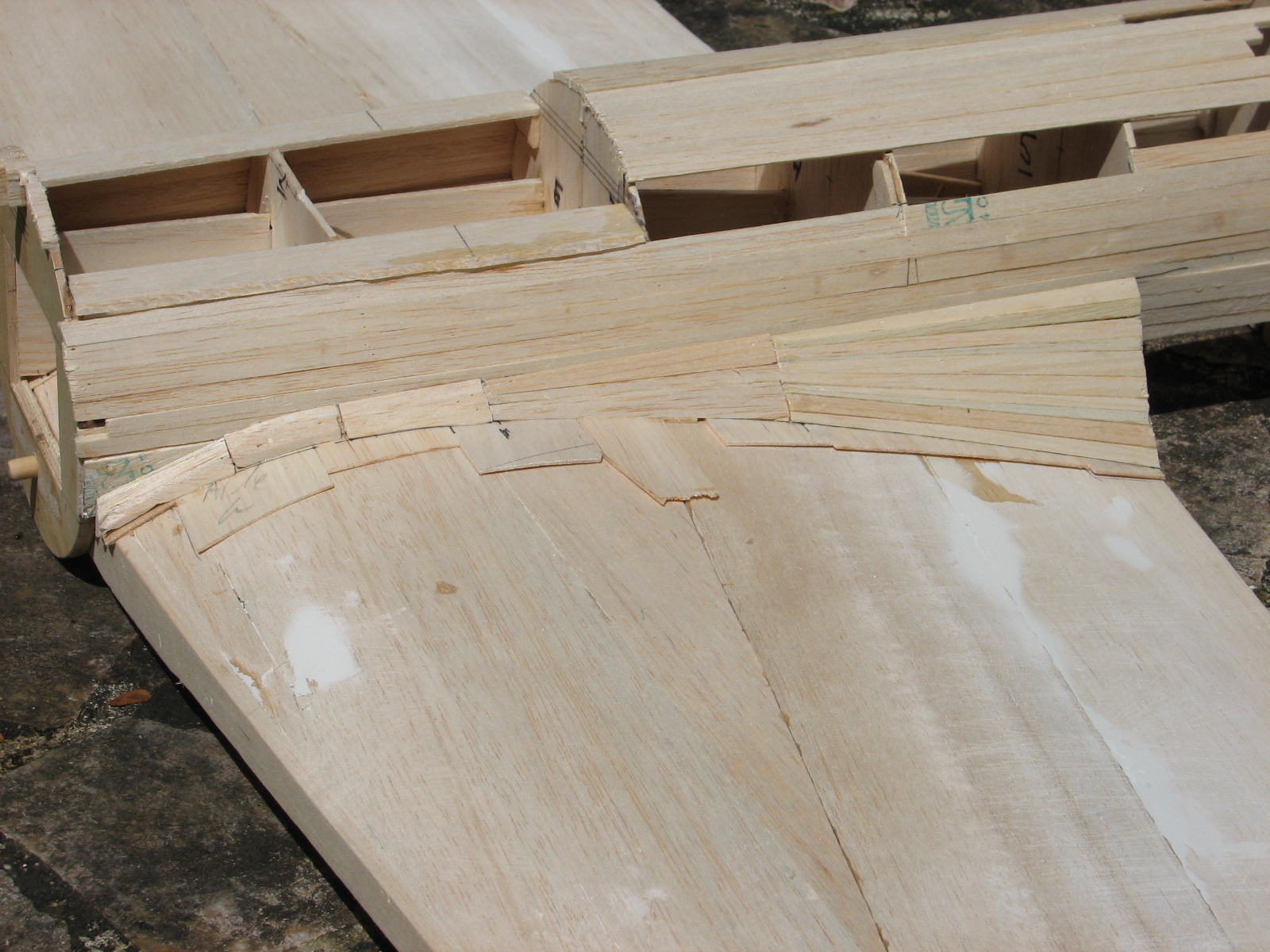
Un peu d'enduit pour cacher la misère :
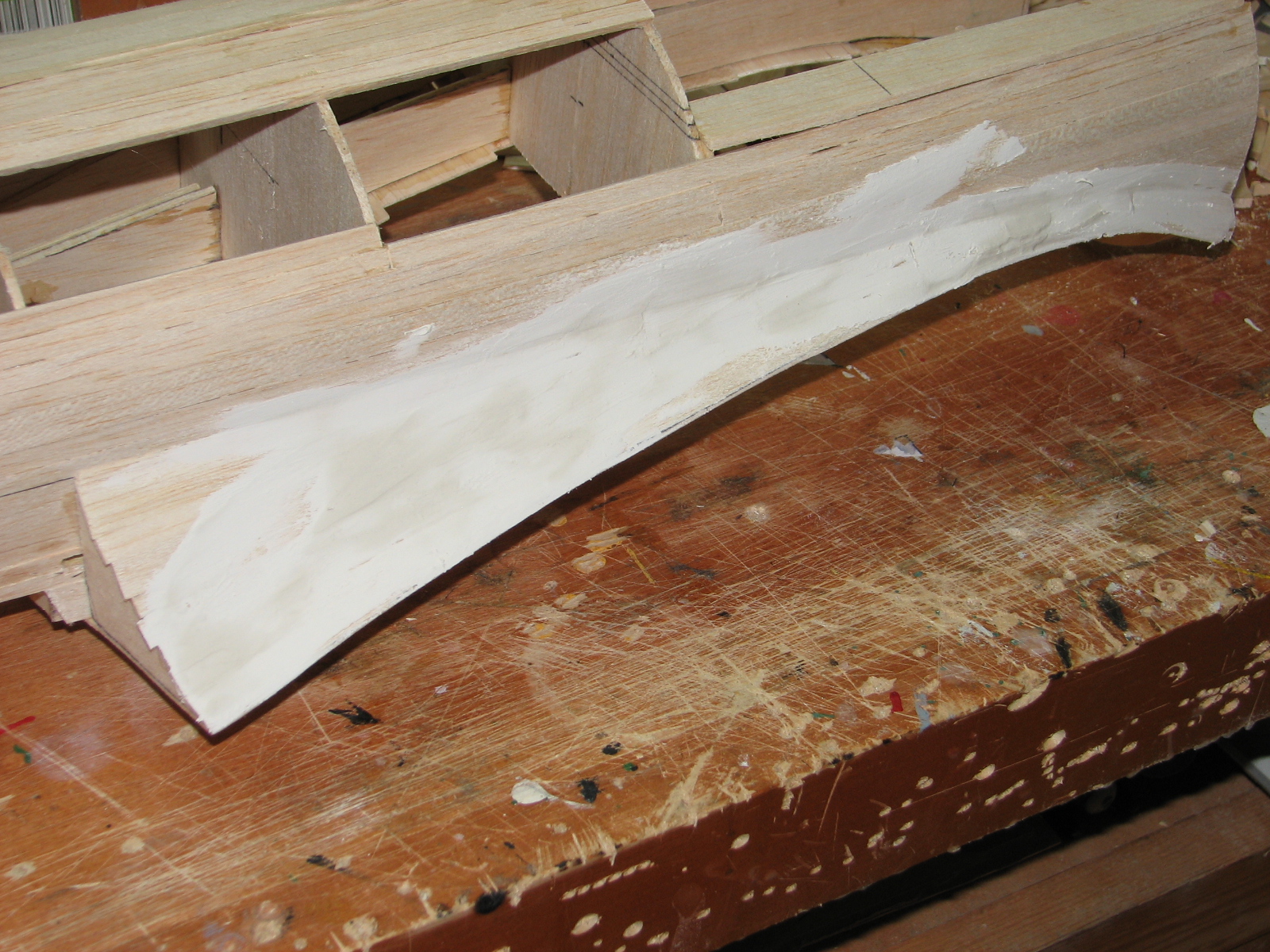
Prochain épisode : ponçage.
>>>>> Haut de page
>>>>> Sommaire : lâatelier de David
>>>>> Page dâaccueil
>>>>> Dernières mises à jour
(2 commentaires)
Passer au formulaire de commentaire